Emerging Trends in Precision CNC Machining for Global Buyers in 2025 and Practical Strategies to Leverage Them
As we look towards 2025, the landscape of precision CNC machining is evolving at a rapid pace, driven by technological advancements and increasing global competition. This industry, which focuses on the intricate and exacting processes of computer numerical control machining, is witnessing emerging trends that are reshaping how manufacturers and buyers approach production and procurement. Understanding these trends is vital for global buyers aiming to stay ahead in their industries and leverage innovations that enhance efficiency, precision, and cost-effectiveness.
In this blog, we will explore these key trends and offer practical strategies for buyers to effectively harness them. From the integration of artificial intelligence and machine learning into CNC processes to the growing importance of sustainable practices and customization, precision CNC machining holds immense potential for transformative change. By strategically adopting these trends, global buyers can not only improve their operational workflows but also gain a competitive edge in an increasingly complex market. Join us as we delve into the future of precision CNC machining and uncover the strategies that will define success in the years to come.
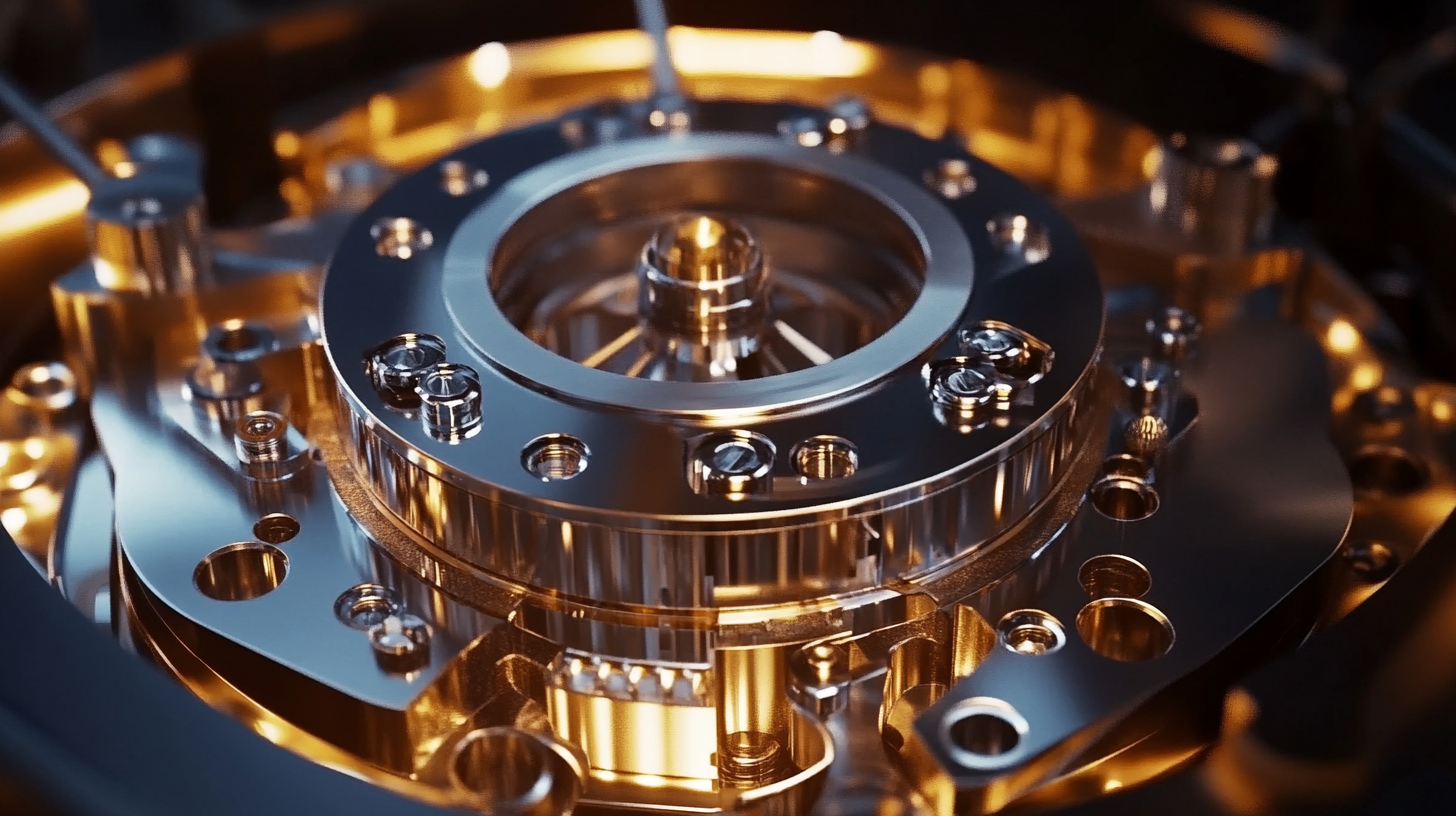
Emerging Technologies in Precision CNC Machining: Key Innovations for 2025
The landscape of precision CNC machining is set to undergo significant transformations by 2025, driven by emerging technologies that promise to enhance efficiency and precision. As industries continue to seek greater accuracy in manufacturing processes, innovations such as advanced robotics, artificial intelligence, and machine learning are becoming cornerstones of modern CNC machining. These technologies are not only automating tasks but also providing real-time data analytics, allowing manufacturers to optimize production workflows and reduce downtime. Additionally, the integration of cloud computing into CNC systems is revolutionizing how data is stored, accessed, and utilized. This allows for seamless collaboration between teams across various geographical locations, facilitating better communication and project management. Moreover, virtual reality is emerging as a powerful tool for training operators, enabling them to simulate machining processes in a safe environment before handling actual machinery. This not only enhances skill acquisition but also minimizes the risk of errors during production. As we move towards 2025, global buyers should stay abreast of these technological advancements to leverage their benefits effectively. Embracing these innovations can lead to improved product quality, reduced production costs, and enhanced competitiveness in the marketplace. By strategically investing in cutting-edge CNC machining technologies, businesses can position themselves to meet future demands and navigate the complexities of the evolving manufacturing landscape.
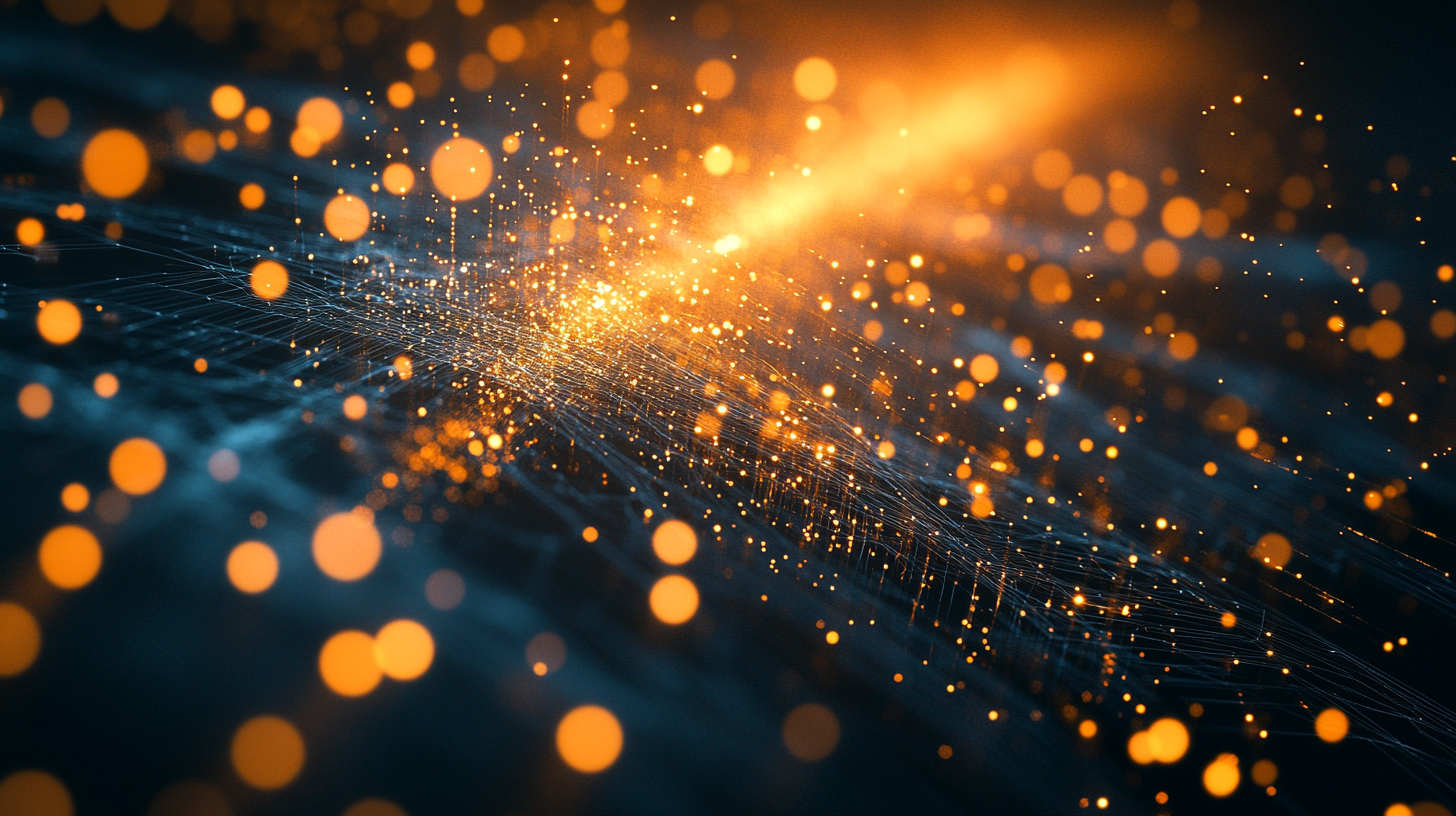
Data-Driven Decision Making in CNC Machining: Leveraging Analytics for Optimal Performance
In the rapidly evolving landscape of precision CNC machining, data-driven decision making stands out as a pivotal trend for global buyers in 2025. A report from MarketsandMarkets projects that the CNC machining market will reach $100 billion by 2025, driven largely by advancements in analytics and automation. This growth underscores the necessity for manufacturers to embrace data analytics in their operations to enhance efficiency and competitiveness.
Leveraging analytics allows businesses to track key performance indicators (KPIs) such as machine uptime, cycle times, and production yields, leading to informed management decisions. According to a study by Deloitte, companies that implement data analytics can see a reduction in operational costs by up to 15%. Such insights enable organizations to optimize their machining processes, leading to increased precision and minimized waste, ultimately enhancing product quality.
Moreover, integrating Internet of Things (IoT) technologies with CNC machines can provide real-time data collection and analysis. A report from Accenture indicates that 70% of manufacturers are already investing in IoT capabilities, which facilitate predictive maintenance and prevent breakdowns. As a result, not only does this enhance machine performance, but it also significantly extends the lifespan of equipment, proving advantageous for the bottom line. By harnessing these data-driven strategies, global buyers can position themselves to take full advantage of emergent trends in precision CNC machining.
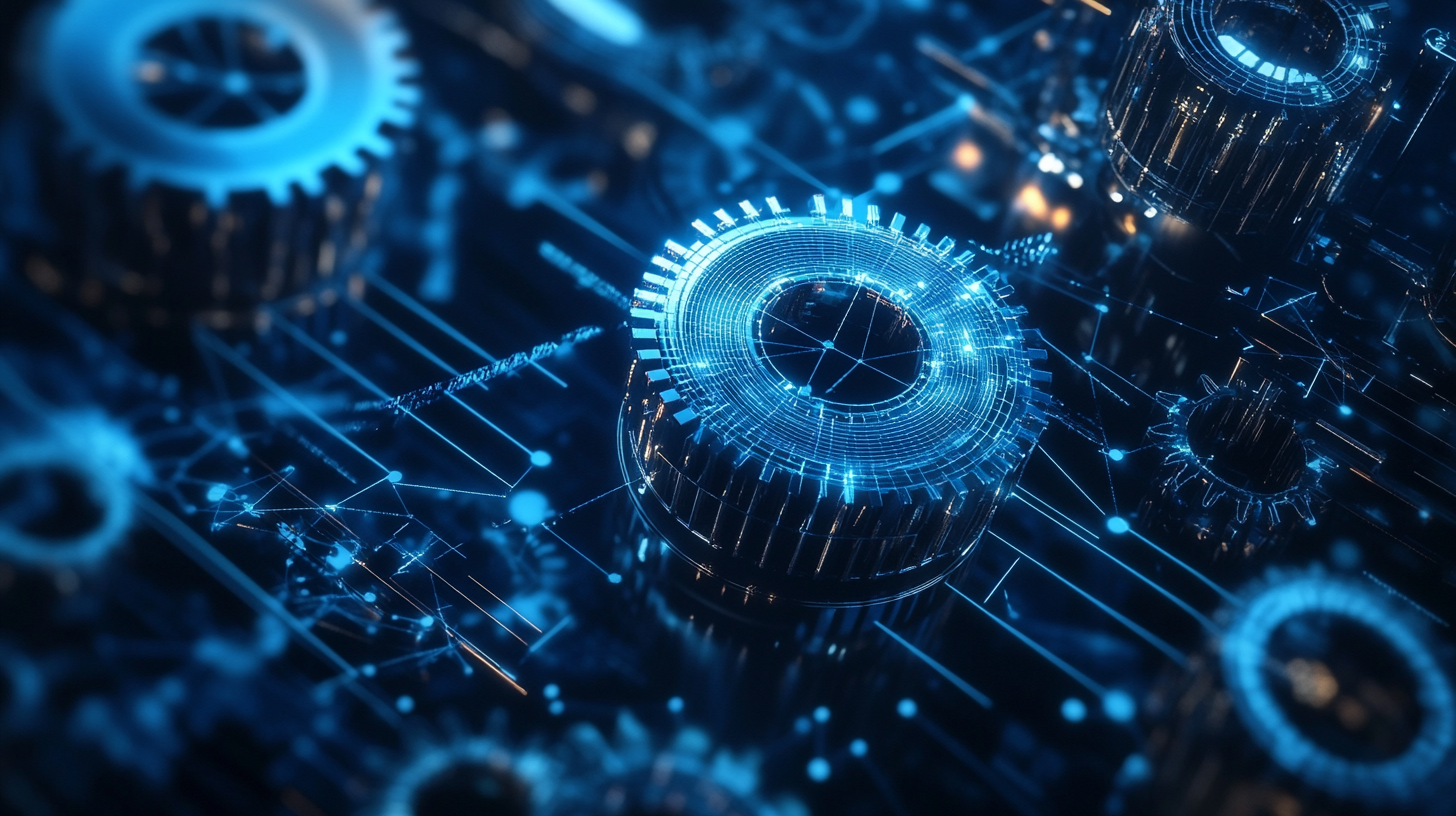
Sustainability in CNC Machining: Eco-Friendly Practices and Their Market Impact
As the global manufacturing landscape evolves, sustainability in CNC machining has emerged as a pivotal trend for 2025. Recent reports indicate that businesses focused on eco-friendly practices can not only comply with regulatory pressures but also gain a competitive edge in the market. For instance, companies that implement sustainable practices are projected to see a market growth rate of 6.5% annually, significantly outpacing those that do not prioritize environmental responsibility.
The IMTS 2024 highlighted innovations such as automation and sustainability practices within CNC machining, emphasizing a shift towards processes that minimize waste and energy consumption. The integration of IoT and AI into manufacturing systems is facilitating more efficient operations, thereby reducing the carbon footprint associated with machining activities. Advanced techniques like sustainable additive manufacturing are gaining traction; this method, driven by digital 3D design, holds the potential to significantly mitigate greenhouse gas emissions, particularly in resource-intensive industries like construction.
In line with global trends, manufacturers are increasingly investing in facilities that prioritize both production efficiency and environmentally conscious practices. For example, ongoing expansions in Chennai aim to enhance production capabilities by 25% while embedding sustainable technologies—demonstrating a clear commitment to responsible manufacturing. As the industry continues to adapt, leveraging these eco-friendly practices will be crucial for buyers seeking to align with market demands and environmental standards in the coming years.
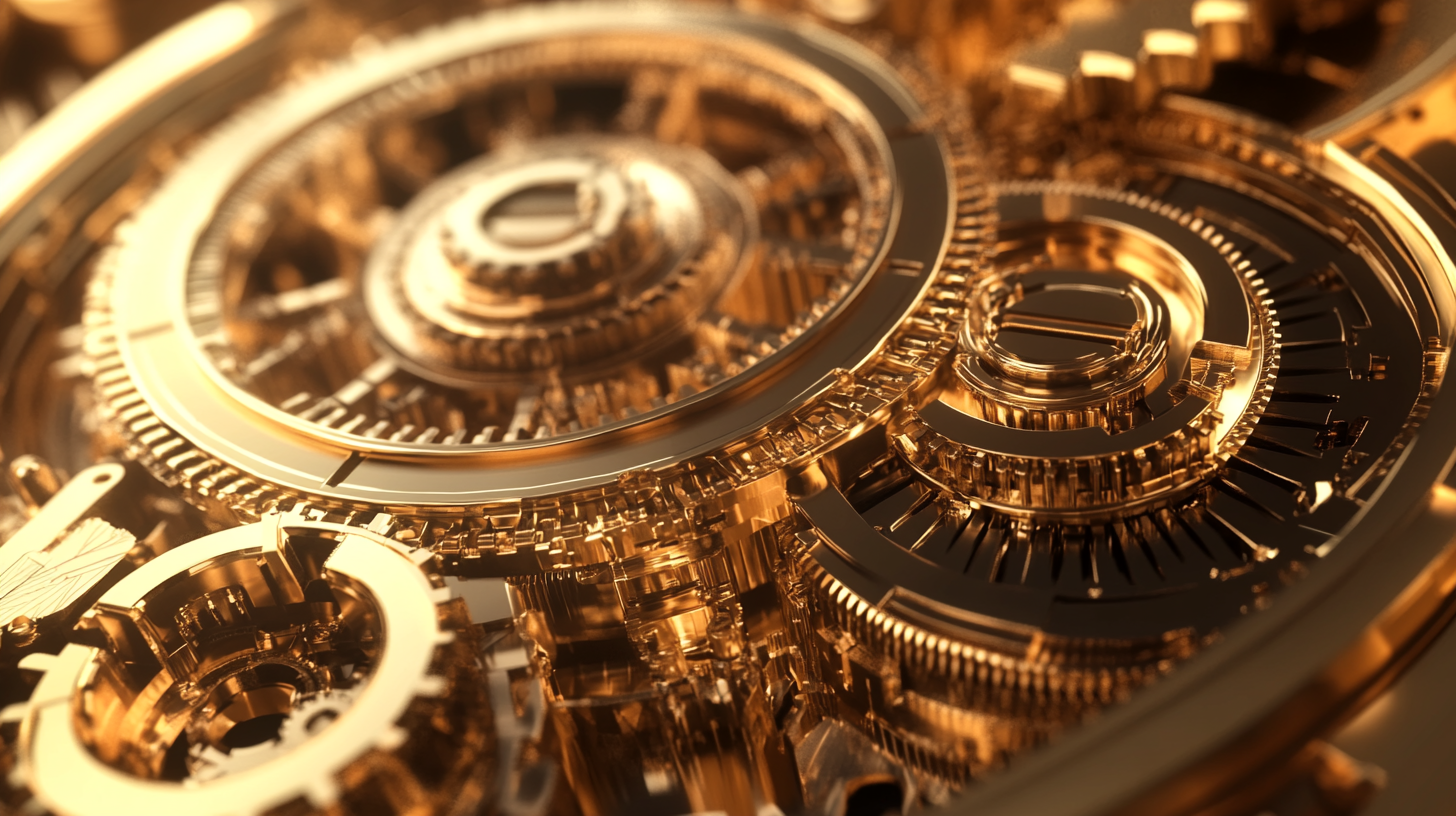
The Role of Automation and Robotics in Shaping Future CNC Machining Efficiencies
As we move towards 2025, the landscape of CNC machining is being significantly shaped by the integration of automation and robotics. These technologies are not just enhancing operational efficiencies but are also addressing critical challenges such as the ongoing shortage of skilled CNC machinists. According to a recent report, the industry is expected to face a talent gap of over 200,000 skilled machinists by 2025, making automation a vital component for sustaining productivity levels.
Robotics in manufacturing is increasingly about more than just mechanization; it represents a shift towards smarter, more agile production environments. Advances in robotic technology allow for higher precision and efficiency, reducing cycle times and waste. Innovations such as collaborative robots (cobots) are designed to work alongside human operators, enhancing capabilities without the need for extensive re-engineering of existing workflows. Reports indicate that businesses adopting robotics are experiencing productivity increases of up to 30%, proving that automation is essential for maintaining a competitive edge in the market.
Additionally, the rise of Industry 4.0 is facilitating the connection of different components within the manufacturing process. Systems designed for smart factory readiness are becoming increasingly important, allowing for real-time monitoring and management of operations. For instance, automated fluid dispensing solutions are being integrated into machining processes to boost efficiency and precision. With technologies such as digital twins and AI-driven analytics gaining traction, manufacturers are poised to leverage these innovations to optimize their workflows and meet the demands of global buyers more effectively.
As we look ahead to a more automated future, it is clear that investing in these technologies will be crucial for businesses aiming to excel in precision CNC machining. Embracing automation isn't just about keeping pace with competitors; it's about leading the charge into the next era of manufacturing.
Competitive Advantages for Global Buyers: Strategic Sourcing and Supplier Partnerships in CNC Machining
In the evolving landscape of CNC machining, global buyers are increasingly recognizing the importance of strategic sourcing and supplier partnerships to maintain a competitive edge. In 2025, the success of businesses in this field will hinge on the ability to foster relationships that not only enhance productivity but also ensure access to the latest technologies and innovations. By prioritizing partnerships with suppliers who embrace emerging trends, buyers can optimize their supply chains and achieve significant cost efficiencies.
To leverage these competitive advantages, global buyers should focus on building collaborative relationships with their suppliers. This means engaging in open communication, sharing market insights, and aligning goals to create a win-win situation. By combining resources and expertise, businesses can explore new machining techniques, better materials, and advanced technologies that drive efficiency. Additionally, investing in joint development initiatives can lead to customized solutions tailored to specific industry needs, setting businesses apart from their competitors.
Moreover, buyers should leverage data analytics and real-time monitoring tools to enhance decision-making capabilities. By analyzing supplier performance and market trends, businesses can make informed sourcing decisions that minimize risks while maximizing quality and reliability. Adopting a proactive approach in managing supplier relationships and utilizing technology will position global buyers to capitalize on the rapidly changing CNC machining landscape, ensuring they remain at the forefront of industry advancements and innovation.
NORTH EASTON MACHINE • 218 Elm Street • North Easton, MA 02356 • 508-238-6219