Revolutionizing Global Supply Chains with Advanced CNC Parts Machining Technologies
In an era where globalization and digital transformation dominate the industrial landscape, the efficiency of global supply chains has never been more critical. According to a report by McKinsey & Company, companies that leverage advanced manufacturing technologies, including CNC parts machining, can achieve up to a 30% reduction in production costs and a significant improvement in delivery times. As the demand for precision and customization rises, CNC parts machining is becoming a cornerstone in manufacturing, enabling companies to respond swiftly to market changes while maintaining high quality standards.
Moreover, a study by Gartner highlights that the integration of CNC machining technologies into supply chain operations can enhance operational agility and reduce lead times by 25%. This evolution is paving the way for manufacturers to not only optimize their processes but also innovate with new materials and designs that were previously unattainable. As we delve into the revolution brought about by CNC parts machining, it is essential to explore how these advanced technologies are reshaping global supply chains and driving competitive advantage in the manufacturing sector.
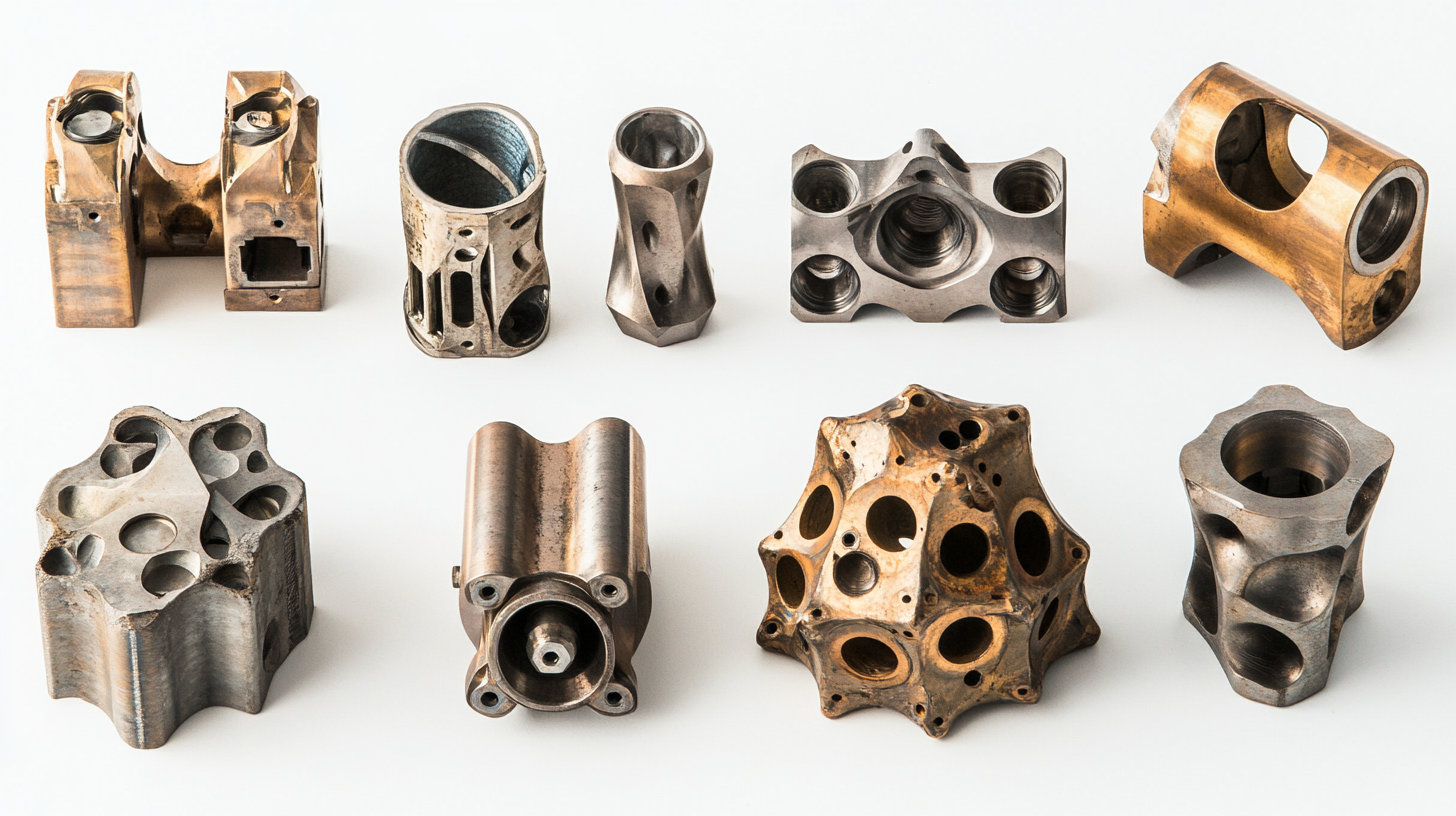
The Role of CNC Machining in Streamlining Global Supply Chain Efficiency
The role of CNC machining in streamlining global supply chain efficiency is becoming increasingly significant as industries adapt to rapid technological advancements. CNC machining technology offers unparalleled precision and efficiency, enabling manufacturers to produce complex parts that are crucial for modern supply chains. As companies face disruptions due to shifting market demands and logistics challenges, the ability to quickly and accurately produce components through CNC machining can enhance overall supply chain resilience. Recent statistics highlight the robust growth of the global CNC machine market, projected to reach $195.59 billion by 2032. This growth can be attributed to the increasing incorporation of advanced manufacturing technologies in supply chain operations. By leveraging CNC machining, manufacturers can minimize production times and reduce waste, ensuring that they meet the fluctuating demands of customers while maintaining cost-effectiveness. Moreover, the integration of artificial intelligence within CNC machining processes further amplifies supply chain efficiency. The use of AI for demand forecasting allows companies to optimize their inventory management and production scheduling, aligning their output with actual market needs. As industries continue to embrace digital transformation, CNC machining will play a pivotal role in enhancing the agility and responsiveness of global supply chains, paving the way for a more sustainable and efficient manufacturing future.
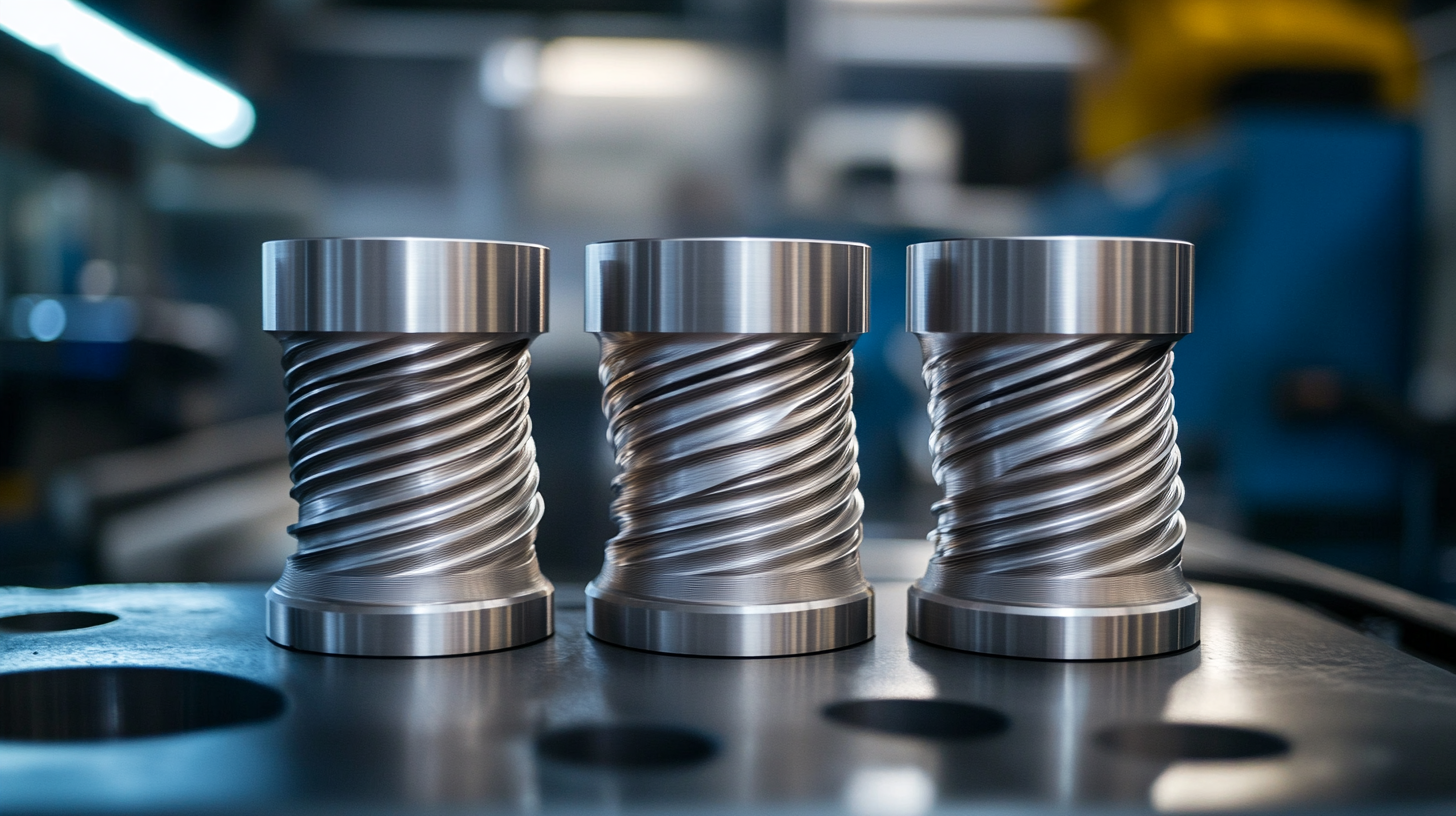
Innovations in CNC Technology Driving Cost Reductions and Quality Enhancements
The landscape of global supply chains is undergoing significant transformation, largely due to innovations in CNC (Computer Numerical Control) technology. These advancements are not just enhancing the efficiency of manufacturing processes but are also driving substantial cost reductions for companies. By automating precision machining, manufacturers can optimize production schedules, minimize material waste, and reduce labor costs. As a result, businesses can achieve economies of scale, which translate into lower prices for consumers and increased competitiveness in international markets.
Moreover, CNC machining technologies are setting new standards for quality enhancement in manufacturing. With advanced features such as adaptive programming and real-time monitoring, manufacturers can produce intricate parts with unparalleled accuracy and consistency. This level of precision is crucial in industries where even the smallest deviation can lead to significant failures, such as aerospace or medical devices. By embracing these innovations, companies can ensure that their products not only meet but exceed industry standards, thereby enhancing customer satisfaction and trust.
In addition to cost and quality benefits, the integration of advanced CNC technologies into supply chains also fosters sustainability. Efficient machining processes reduce energy consumption and waste generation, allowing companies to align with environmental standards and consumer expectations for sustainable practices. As businesses continue to navigate the challenges of global supply chains, the adoption of cutting-edge CNC machining technologies presents a viable path towards operational excellence and responsible production.
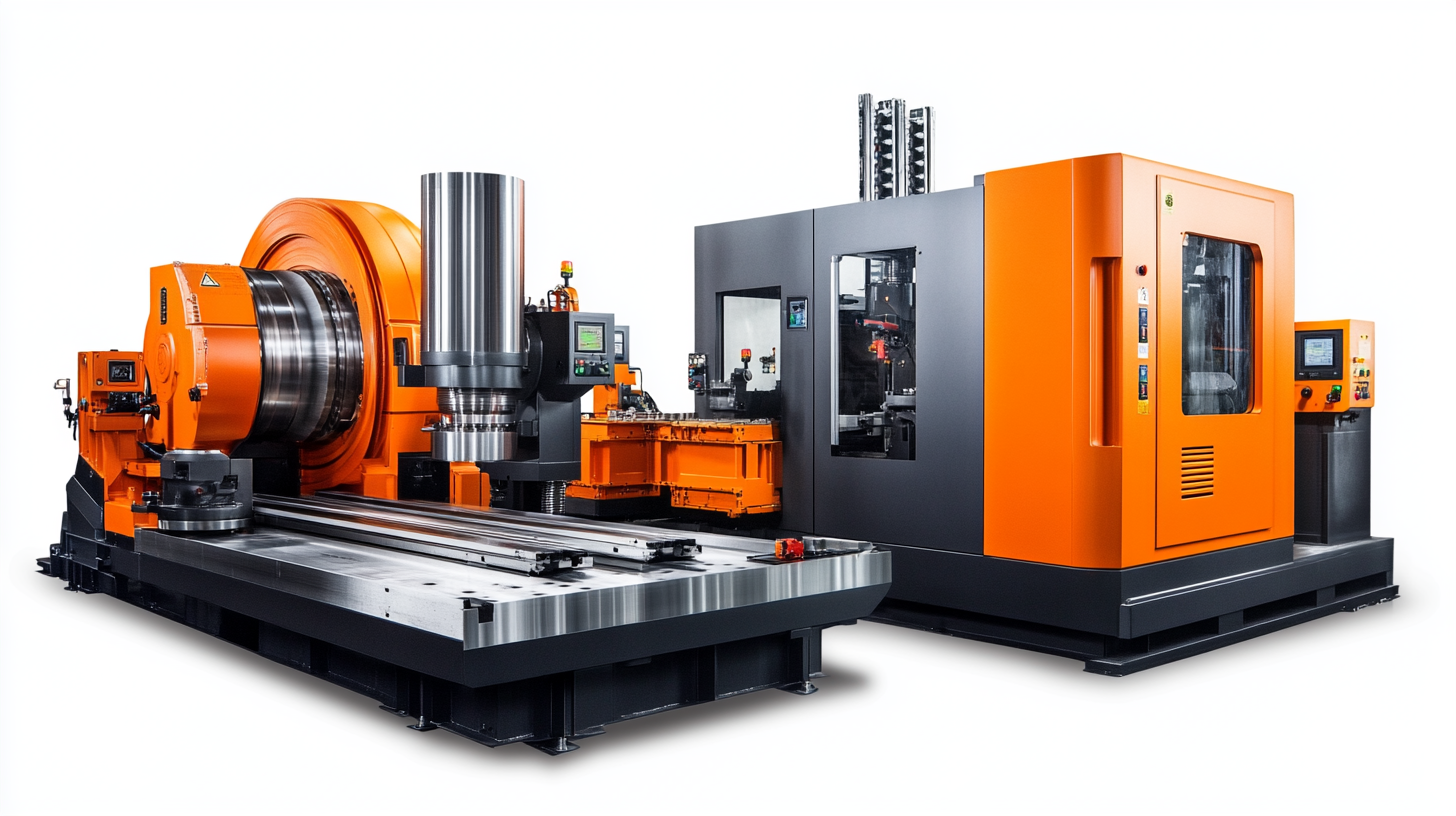
Case Studies: Successful Implementation of CNC Parts in Various Industries
In today's rapidly evolving industrial landscape, advanced CNC parts machining technologies have become a game changer across various sectors. From aerospace to automotive, these technologies have been successfully implemented, illustrating their potential to enhance productivity, precision, and overall efficiency. For instance, a leading aerospace manufacturer showcased how CNC machining allowed for the rapid production of lightweight components, drastically reducing lead times while maintaining stringent quality standards. By integrating sophisticated software and automation, they not only streamlined their supply chain but also minimized waste, leading to cost savings and improved sustainability.
In the automotive industry, a renowned car manufacturer embraced CNC machining to innovate their production process. By utilizing multi-axis CNC machines, they could produce complex parts that were previously labor-intensive and time-consuming to create. This shift not only accelerated their production rate but also enabled them to customize designs with greater accuracy. As a result, they were able to respond quicker to market demands, demonstrating that advanced machining technologies can create a competitive edge in a fast-paced industry.
Moreover, the medical sector has started harnessing CNC machining for the production of intricate surgical instruments and prosthetics. One healthcare company implemented CNC technology to achieve unprecedented levels of precision in their products, significantly improving patient outcomes. The ability to produce bespoke parts tailored to individual patient needs has revolutionized their supply chain, allowing for faster turnaround times without sacrificing quality. These case studies across different industries highlight the transformative power of CNC parts machining, emphasizing its vital role in optimizing global supply chains.
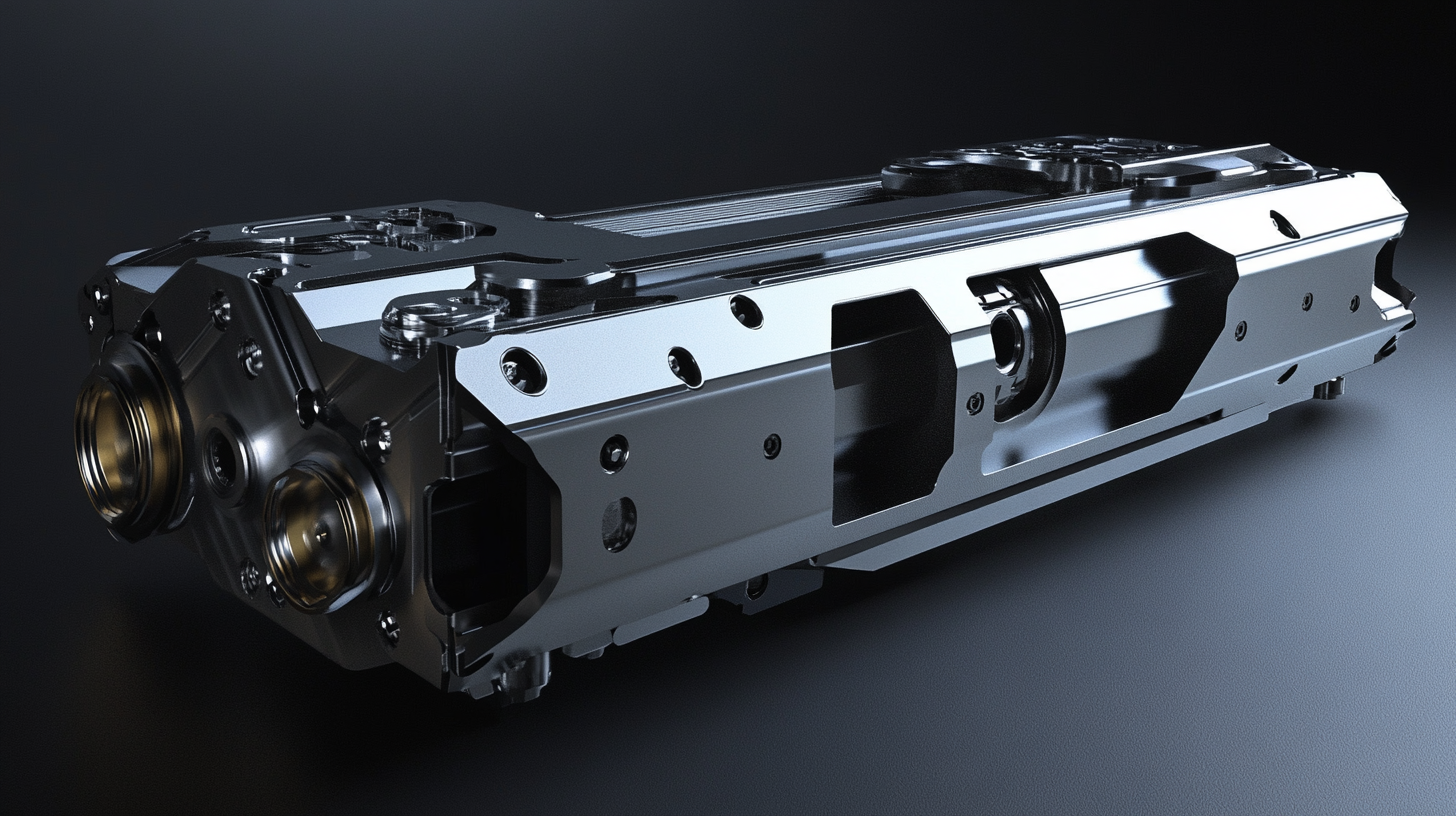
Future Trends: How CNC Machining Will Shape Supply Chains Globally
The advancement of CNC machining technologies is set to significantly influence global supply chains, creating a ripple effect across industries. According to a report by MarketsandMarkets, the global CNC machines market is projected to grow from $69.93 billion in 2021 to $99.29 billion by 2026, achieving a compound annual growth rate (CAGR) of 7.6%. This growth is driven by the increasing demand for precision and customization in manufacturing, which is fundamental for optimizing supply chain efficiency.
One of the most critical trends is the integration of Industry 4.0 technologies into CNC machining processes. As manufacturers adopt smart technologies, real-time data analytics will enable more agile and responsive supply chains. A McKinsey report highlights that companies leveraging data analytics and IoT technologies can improve their supply chain forecasting accuracy by up to 50%. This level of precision supports lean manufacturing practices, reducing waste and inventory costs, ultimately enhancing overall performance.
Furthermore, the rising emphasis on sustainability is pushing manufacturers to utilize advanced CNC machining techniques that minimize material waste and energy consumption. Research from Deloitte indicates that 75% of manufacturing companies are actively focusing on sustainability, with CNC machining offering solutions such as additive manufacturing and more efficient production processes. This alignment with sustainability not only meets regulatory requirements but also resonates with consumers, laying the groundwork for a more responsible global supply chain paradigm.
Challenges and Solutions in Adopting Advanced CNC Technologies in Supply Chains
The adoption of advanced CNC machining technologies is reshaping global supply chains, yet it comes with a unique set of challenges that companies must navigate. As the global CNC machine market is projected to grow from $101.22 billion in 2025 to $195.59 billion by 2032, with a compound annual growth rate (CAGR) of 9.9%, businesses need to strategically position themselves to leverage this growth while addressing operational hurdles.
One significant challenge is the integration of these advanced technologies into existing supply chain frameworks. Companies often face resistance to change from traditional processes and a workforce lacking the necessary digital skills. Additionally, supply chain disruptions caused by external factors—such as geopolitical tensions and pandemics—add layers of complexity to the adoption of CNC machining innovations. To mitigate these risks, organizations are increasingly looking towards artificial intelligence and digital twin technologies, which enhance data analytics and forecasting capabilities, enabling more agile and resilient supply chain operations.
Another critical aspect is ensuring sustainability throughout the manufacturing process. As global attitudes shift towards environmental accountability, manufacturers are pressured to minimize waste and energy consumption. The integration of sustainable practices not only meets regulatory demands but also appeals to a conscientious consumer base. By overcoming these challenges and embracing advanced CNC machining technologies, companies can position themselves as leaders in the evolving manufacturing landscape and ensure effective supply chain management.
NORTH EASTON MACHINE • 218 Elm Street • North Easton, MA 02356 • 508-238-6219