Discovering Reliable Suppliers with Effective Strategies for Cnc Machining Success
In the ever-evolving landscape of manufacturing, CNC machining stands out as a game-changing technology that enables precision and efficiency in production. However, the success of any CNC machining operation heavily relies on the selection of reliable suppliers. With the right partners, businesses can optimize their processes, enhance product quality, and ultimately drive greater profitability. Discovering these dependable suppliers is no simple task; it requires a strategic approach that encompasses thorough research, robust evaluation, and ongoing relationship management.
This blog aims to equip manufacturers with effective strategies for identifying and securing reliable suppliers in the CNC machining sector. By leveraging industry insights and best practices, companies can navigate the complexities of the supply chain, ensuring they collaborate with suppliers who meet their high standards for quality and reliability. Join us as we delve into essential tips and tactics that will pave the way for successful CNC machining endeavors and foster lasting supplier relationships that can withstand the test of time.
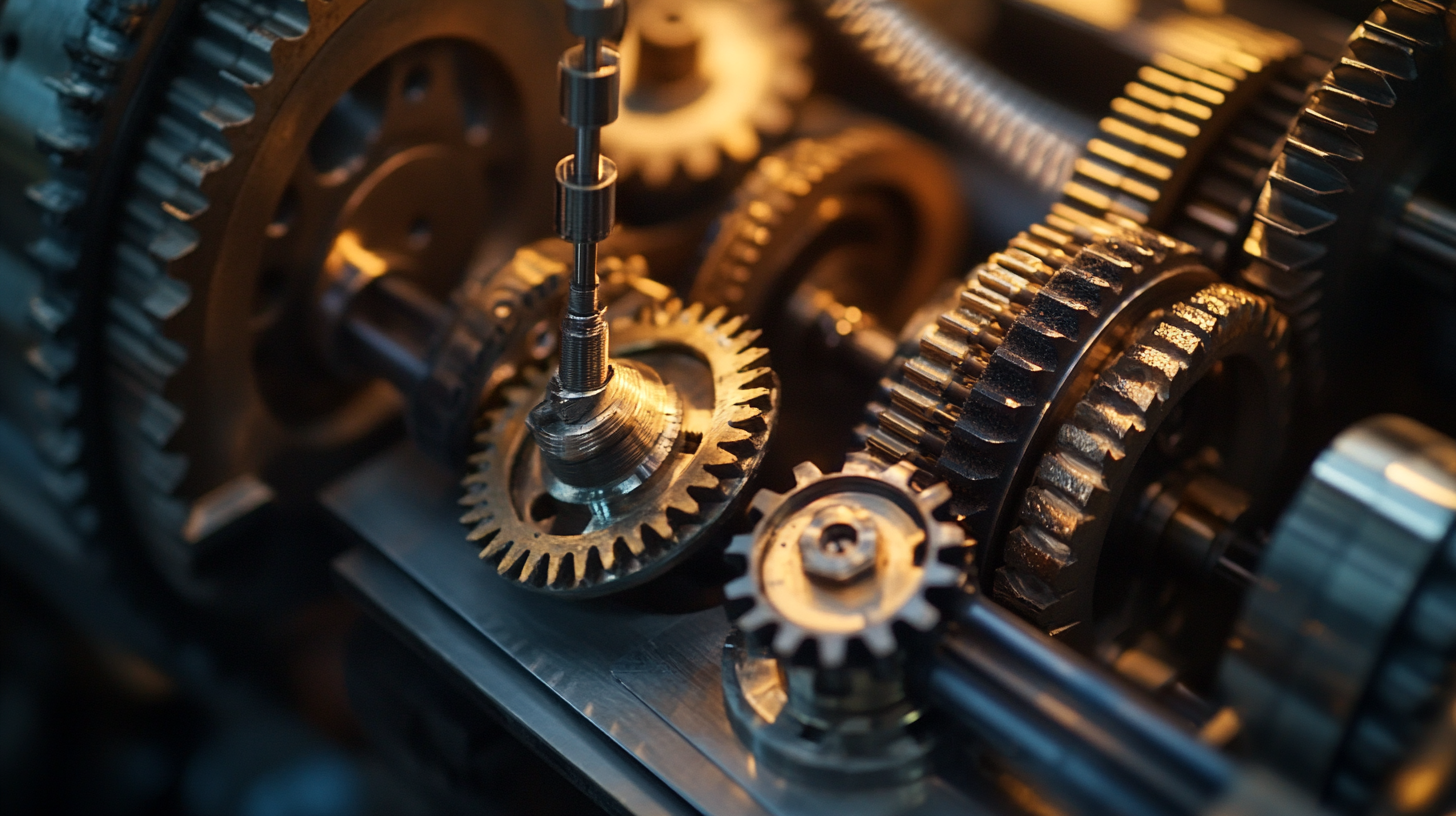
Understanding the Importance of Supplier Reliability in CNC Machining
In the world of CNC machining, the reliability of suppliers plays a crucial role in ensuring the success of any project. When manufacturers partner with dependable suppliers, they can be confident that the materials and components required for machining processes will arrive on time and meet stringent quality standards. This reliability significantly reduces the risk of production delays and costly rework, allowing businesses to maintain a consistent workflow and meet their deadlines with ease. Moreover, reliable suppliers contribute to the overall efficiency of CNC machining operations. By establishing strong relationships with suppliers who understand the specific needs of their clients, manufacturers can benefit from improved communication and faster response times. This collaboration fosters a proactive approach to problem-solving and innovation, enabling manufacturers to adapt to changing market demands. In contrast, unreliable suppliers can lead to a chain reaction of complications, distracting companies from their core competencies and hindering their ability to compete effectively in the industry. Ultimately, understanding the importance of supplier reliability in CNC machining is vital for organizations aiming for sustainable growth. Investing time and resources into building a solid network of trusted suppliers can elevate the quality of finished products, enhance customer satisfaction, and solidify a company's reputation in the market. As CNC machining continues to evolve, the foundational principle of supplier reliability will remain a key determinant of long-term success.
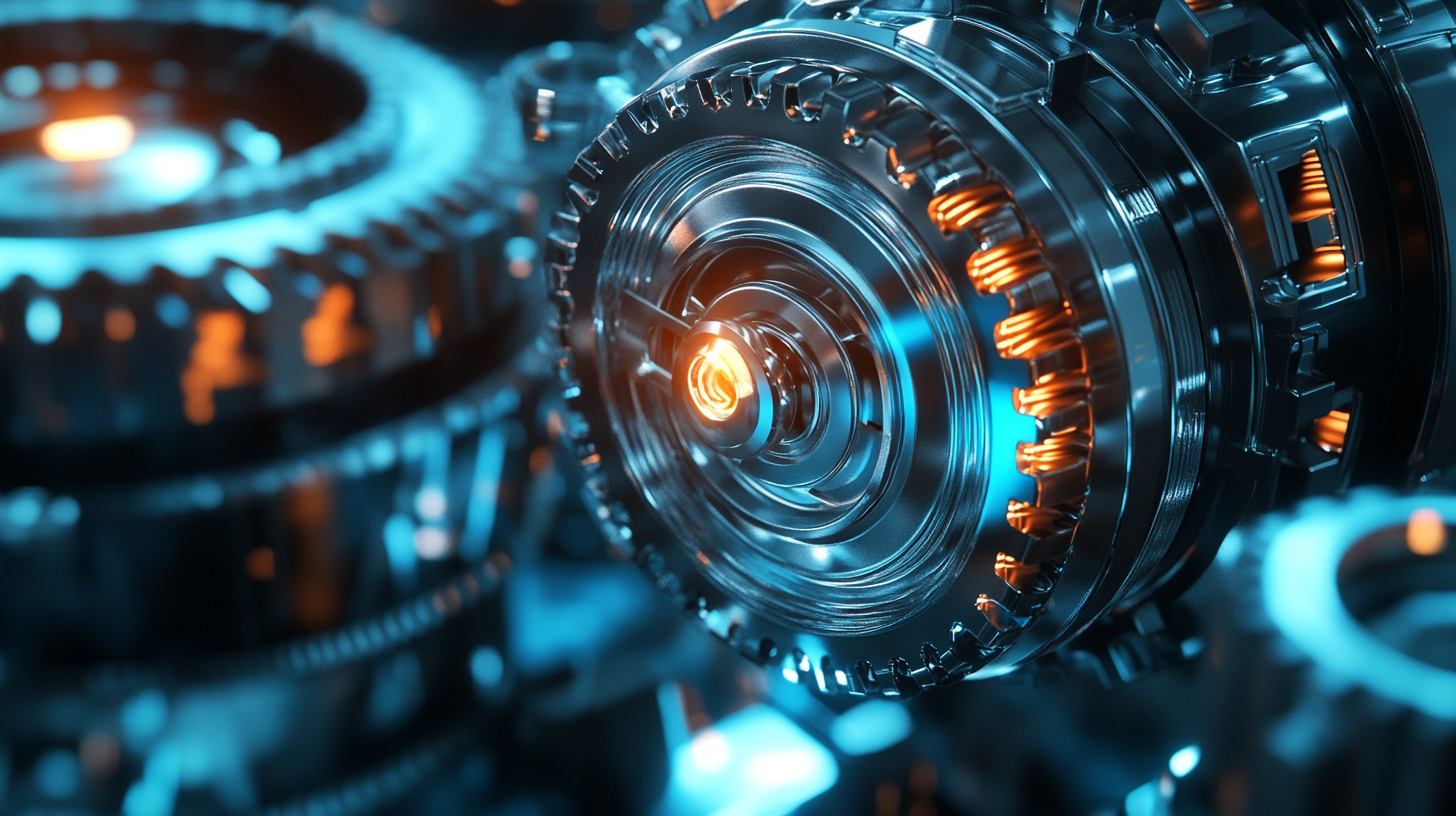
Key Metrics for Evaluating CNC Machining Suppliers
When it comes to CNC machining, selecting the right suppliers is crucial for ensuring high-quality output and operational efficiency. Key metrics for evaluating CNC machining suppliers can significantly influence your production outcomes. According to a report by the International Special Tooling and Machining Association (ISTMA), quality is the top priority for 77% of manufacturers in selecting a supplier. This emphasizes the need to assess a supplier's quality assurance processes and certifications, such as ISO 9001, which ensures adherence to international quality management principles.
Another critical metric is delivery performance. A study from the Association for Manufacturing Technology (AMT) reveals that nearly 60% of companies experience delays due to unreliable suppliers, leading to disruptions in production schedules. Evaluating on-time delivery rates can help identify suppliers who consistently meet deadlines, ultimately facilitating smoother operations. Utilizing data analytics tools to track delivery performance can provide actionable insights and aid in supplier selection.
Cost-effectiveness is also a significant consideration highlighted in a report by the Boston Consulting Group (BCG), which indicates that 45% of manufacturing firms face pressures to lower costs without compromising quality. When assessing suppliers, it is essential to analyze not just the initial pricing but the total cost of ownership, which includes production quality, rework, and potential downtime caused by inferior supplies. Focusing on these key metrics will enable manufacturers to build reliable partnerships with CNC machining suppliers and promote overall business success.
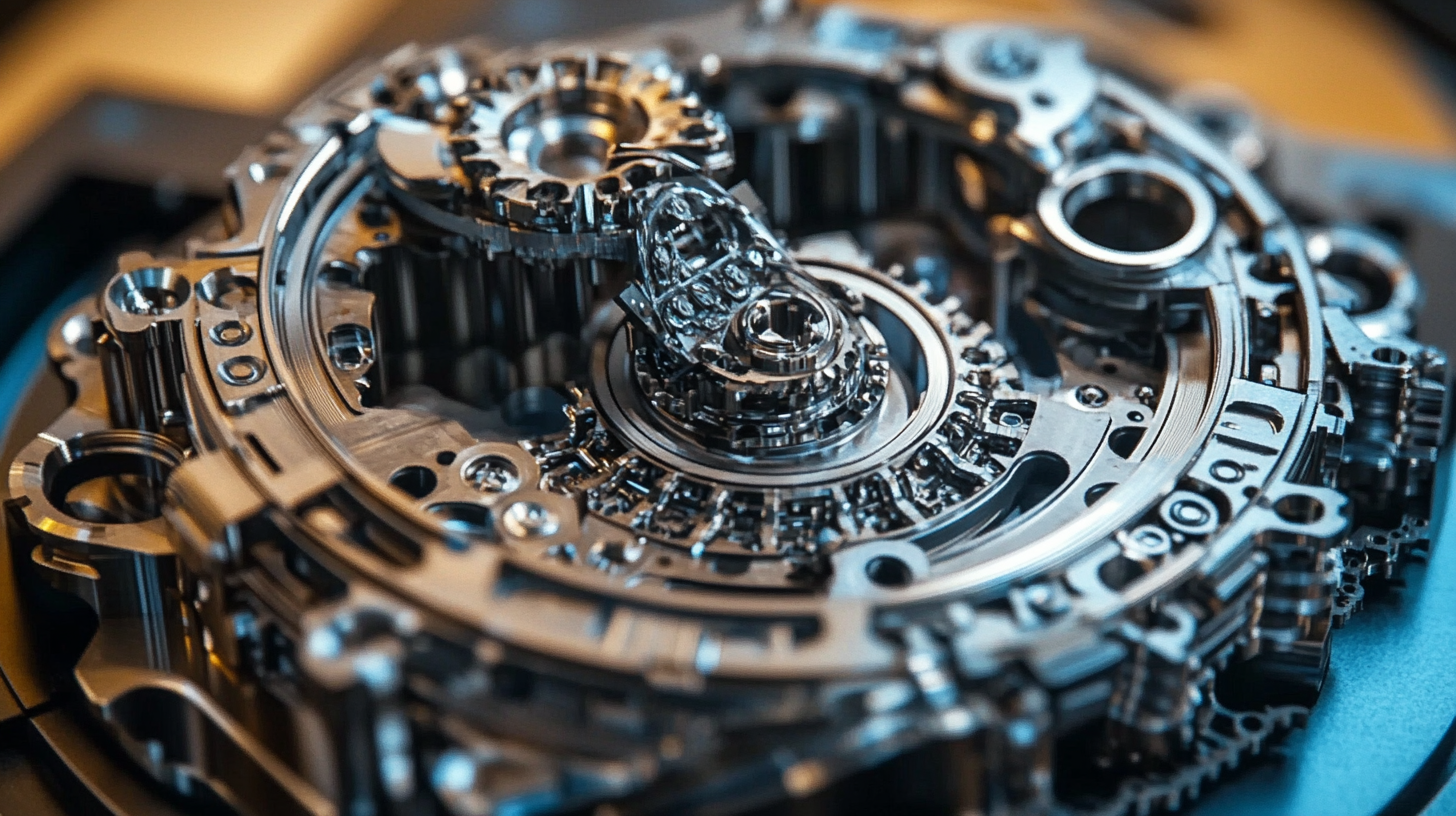
Top Strategies for Identifying Quality CNC Machining Partners
Finding the right CNC machining partner can significantly impact your production quality and efficiency. One of the top strategies for identifying reliable suppliers involves conducting thorough research. Start by exploring online directories, industry forums, and platforms like LinkedIn to compile a list of potential suppliers. Pay attention to their expertise, technological capabilities, and any reviews or testimonials from previous clients. This groundwork will help you narrow down your options and ensure that you’re working with companies known for their quality and reliability.
Another effective approach is to assess the suppliers through direct communication. Initiate conversations with potential partners to gauge their responsiveness and willingness to collaborate. During these discussions, ask about their manufacturing processes, quality control measures, and delivery timelines. This dialogue not only provides insight into their operations but also helps establish rapport, a crucial component in any successful business relationship. Additionally, consider requesting samples or conducting pilot runs to evaluate their work firsthand before committing to larger orders.
Finally, don't overlook the importance of visiting suppliers' facilities, if possible. An onsite visit allows you to see their equipment, processes, and working conditions, giving you a clearer picture of their capabilities. This firsthand experience can reveal a lot about their commitment to quality and innovation. By employing these strategies, you can confidently identify quality CNC machining partners who will contribute to your success.
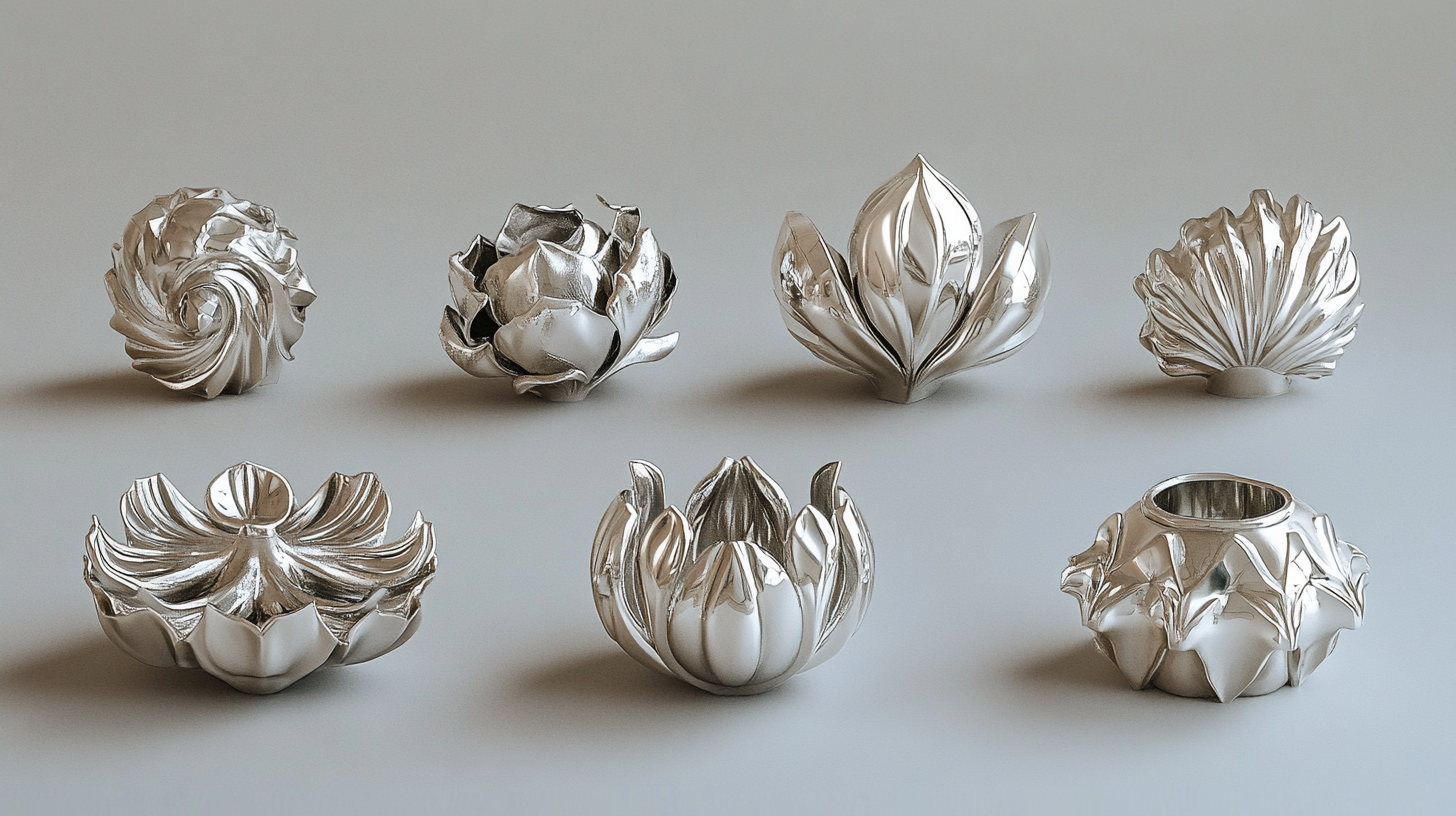
The Role of Certifications and Standards in Supplier Selection
When it comes to CNC machining, the selection of reliable suppliers is crucial for achieving success in production. A key aspect of this selection process is the role of certifications and standards. Certifications, such as ISO 9001, serve as an assurance that a supplier adheres to globally recognized quality management principles. These certifications not only reflect a supplier’s commitment to quality but also their capability in managing complex manufacturing processes. By prioritizing suppliers with recognized certifications, businesses can mitigate risks associated with production errors and material inconsistencies.
Moreover, industry-specific standards play an essential role in supplier selection. For instance, compliance with ASTM or ASME standards can indicate that a supplier meets the technical and material qualifications necessary for CNC machining. These standards ensure that the components produced will perform reliably under operational constraints. By leveraging this information, manufacturers can enhance their product development cycle, ensuring that components will fit seamlessly into larger assemblies without the need for costly rework or redesigns.
Ultimately, choosing suppliers based on their certifications and adherence to established standards is a proactive strategy that can significantly enhance the efficiency and quality of CNC machining operations. By investing time in evaluating these factors, companies can forge partnerships that drive innovation and competitive advantage in the market.
Leveraging Data Analytics for Supplier Performance Assessment
In today's competitive manufacturing landscape, leveraging data analytics for supplier performance assessment has become crucial for achieving CNC machining success. By employing advanced analytical tools, businesses can monitor various metrics that reflect supplier efficiency, quality, and reliability. This process not only aids in selecting the right suppliers but also allows for continuous performance evaluation. Strategies like predictive analytics can help identify potential risks, enabling companies to mitigate issues before they escalate, thus ensuring seamless operations.
The recent trend towards supply chain transparency further underscores the importance of data analytics in supplier management. By making information readily accessible and understandable, manufacturers can foster trust and collaboration with their suppliers. Techniques for enhancing transparency, such as implementing real-time data sharing platforms, can facilitate a better understanding of supply chain dynamics. In this context, innovations like AI-driven solutions, as showcased by leading companies like JD.com, exemplify how organizations can utilize big data to tackle supplier management challenges effectively. By integrating data analytics into their operations, manufacturers not only streamline their supply chains but also unlock new growth opportunities in the global market.
NORTH EASTON MACHINE • 218 Elm Street • North Easton, MA 02356 • 508-238-6219