Unlocking Precision in Cnc Cutting with Advanced Technical Specifications for Global Buyers
While much is changing in manufacturing, perhaps nothing remains more unchanged than the different parameters that define CNC cutting in the architectural sense. Another studious market report by MarketsandMarkets states, for example, that the CNC machining market will be worth $100 billion in 2025, on the back of a burgeoning demand for high-accuracy components across aerospace, automotive, electronics and other such industries. The sophistication of CNC cutting technology is key to fulfilling such demands: It permits manufacturers to implement very intricate designs with great accuracy and on-time production efficiency. As such technical sophistication becomes a crucial aspect for a buyer listed among key constraints to enhanced production capabilities, the suppliers must take time to promote this very focus to them.
And a recent study from Grand View Research finds that CNC cutting is also being driven by growing automation and increasingly by Industry 4.0. Industries are becoming dependent on smart, connected devices for operational improvements and precision enhancement. The deeper we dive into the intricacies of CNC cutting, it becomes quite evident that staying updated on these advancements becomes very important for any organization wanting to maintain their standing in an increasingly competitive global market. This blog aims to elaborate on how unlocking precision in CNC cutting through advanced technical specifications is beneficial for global buyers in streamlining informed decisions regarding their manufacturing processes.
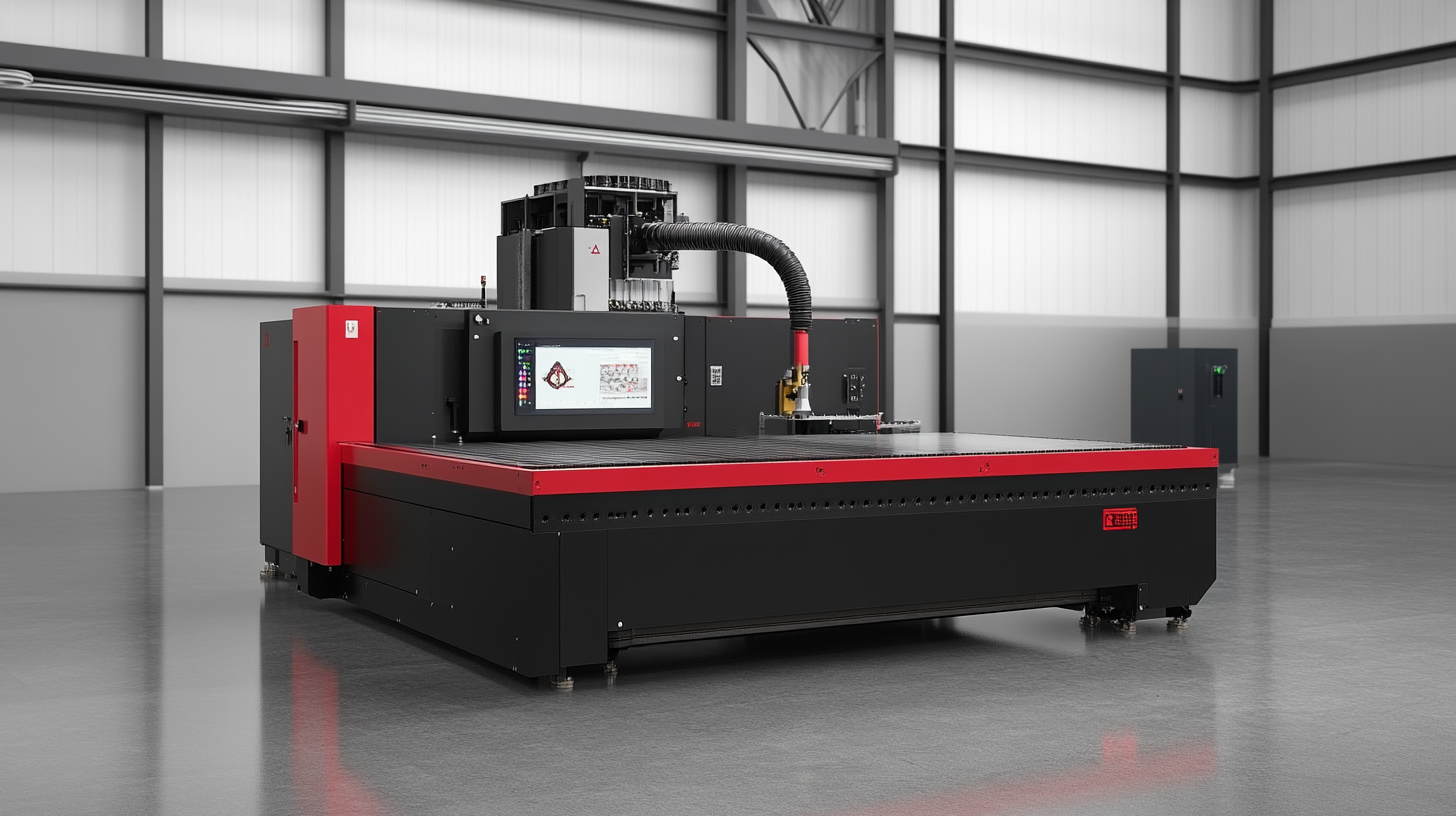
The Importance of Accurate Technical Specifications in CNC Cutting
The accuracy of specification becomes not overstated when it comes to CNC cutting technology. Exact specifications become the basis for the performance and quality machining processes. According to a report published by the International Federation of Robotics in 2022, precise implementing technical parameters increased efficiency by 30 percent in operation, much related to cause. The criticality of this evidence points to documenting everything down so that manufacturers can reach very demanding standards yet waste and reduce downtime at the same time. On top of that, this also means huge money losses. Market Research Future has conducted a study that revealed that 15 percent of revenues can actually be lost because of quality-linked specifications not being debatable. Said that locking up the right specifications would reduce this risk investment for users on reliable production cycles and led to increased confidence for suppliers and their clients. The benefits, therefore, do not end at the operational level but extend to the global market as well. Having accurate performance metrics could give a company a much sharper competitive edge, especially in regions such as Europe and North America, where precision manufacturing rules. This clearer set of technical specifications would smooth the way for international collaboration, inviting advanced technological partnerships and promoting innovation in CNC cutting technologies. In this globalized market, accuracy in specifying technical requirements stands as a linchpin in propelling quality and efficiency across different production environments.
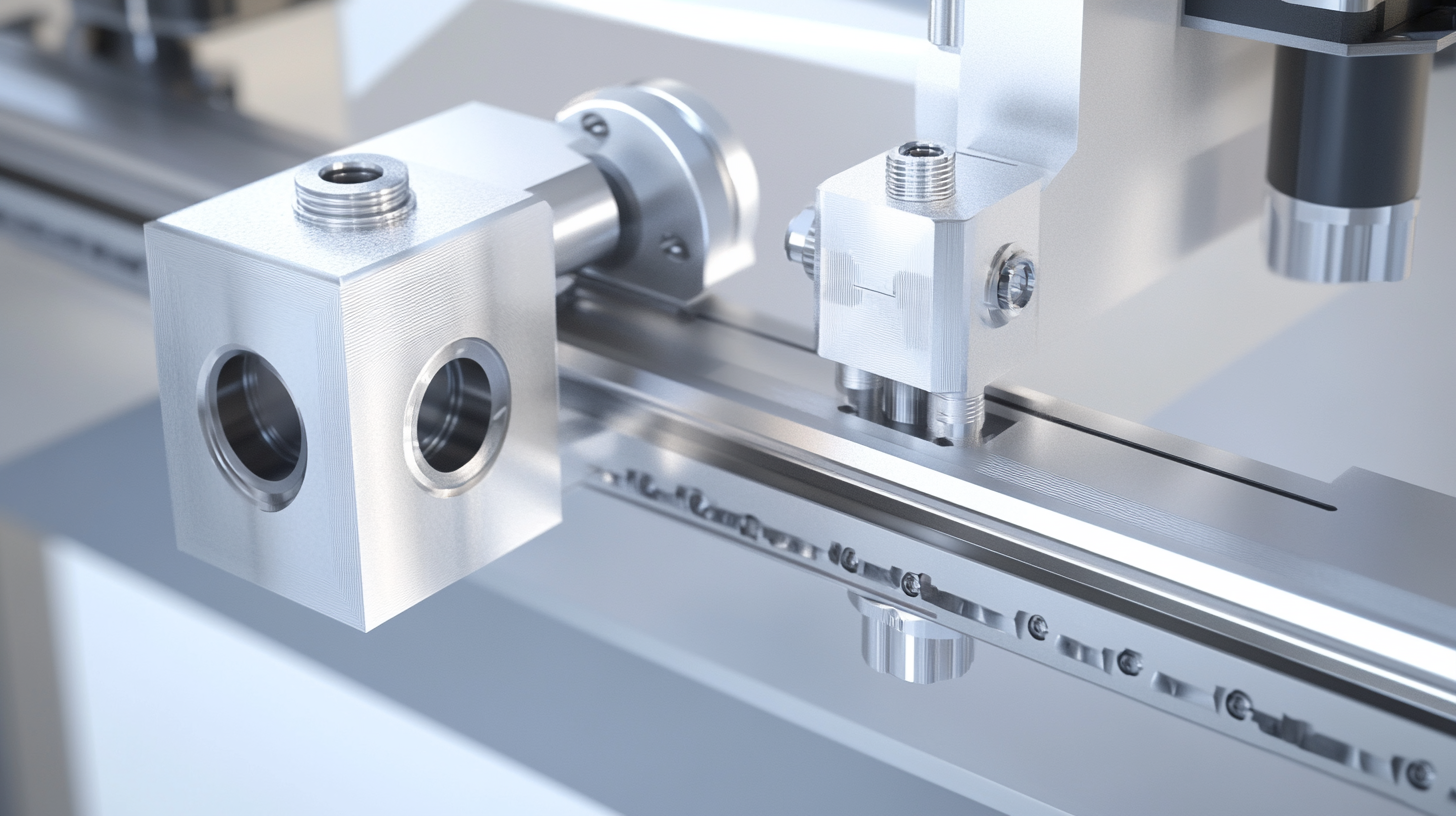
Key Features to Look for in Advanced CNC Cutting Machines
In the ever-growing world of CNC cutting, picking the right kind of machine is of utmost importance for precision and efficiency. An understanding of the advanced features of CNC cutting machines can benefit global clients to a significant degree in enhancing the productivity and quality of what is expected from them. One of the main things to consider on the machine is the maximum cutting speed. The IBISWorld report projects the global CNC machine market trend at a CAGR of 7.5%, eight interests of which will likely be cutting speeds and capability.
Yet another critical aspect is that of the precision, usually expressed in microns. Modern CNC machine holds a positioning accuracy of ±0.01mm to guarantee that the intricate designs are executed with precision. The International journal of Advanced Manufacturing Technology revealed that machines with superbly exact technical specifications had undergone less waste, up to 20%, and resulted overall in lower cost of operation for the businesses.
Additionally, versatility is key to CNC machines. Advanced models handle various materials, such as metals, plastics, and composites. This adaptability means that manufacturers can now take on a mix of jobs using just one CNC machine rather than a whole set of dedicated units. A report compiled by Deloitte states that companies using multi-material CNC take 15% less turnaround time on projects, making them wise investments for global contractors who might view such machines as good long-run investments that are also well laden with competitive advantages.
Integration with Industry 4.0 technologies, such as AI and IoT, is being crucial. This enables real-time monitoring and predictive maintenance, optimize productivity. A study by MNK Global Institute indicated that with smart CNC technology, manufacturers can achieve up to 30% greater operational efficiency within the impending global market landscape.
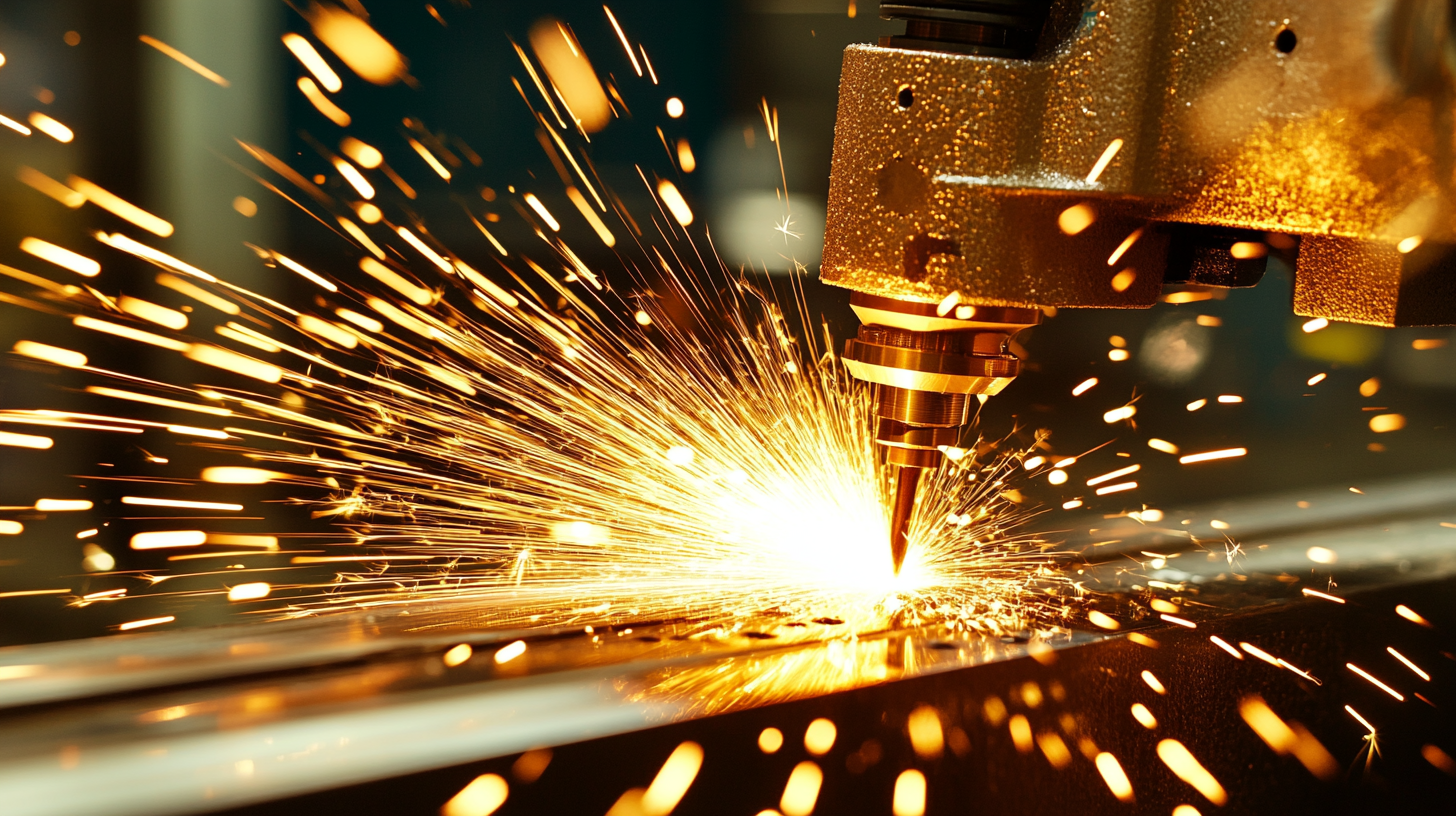
How Global Buyers Can Ensure Quality in CNC Cutting Processes
Buyers for CNC cutting face the quality challenge with exposure to varied manufacturing standards and specifications. The first step toward assuring quality is to perform thorough due diligence on prospective suppliers. Buyers have to seek out manufacturers with ISO certifications and verifiable records in manufacturing precision cutting components. This not only reflects adherence to industry standards but also demonstrates a commitment to the abiding quality of production.
Buyers must know the technical specifications related to their specific requirements. Being aware of the tolerances and material properties as well as tooling capabilities is of utmost importance. With this knowledge in hand, buyers would be able to express their requirements fully to their respective suppliers and also have a common platform for expectations on both sides. Regularly conducting audits of the quality system and inviting suppliers for on-site inspections would help enhance some transparency and build trust and confidence.
The combination of advanced technical specifications with open communication will open unprecedented precision levels in CNC cutting amongst global buyers. This partnership will strengthen the quality of manufactured items and guarantee longer-term partnership agreements in a highly competitive manufacturing environment.
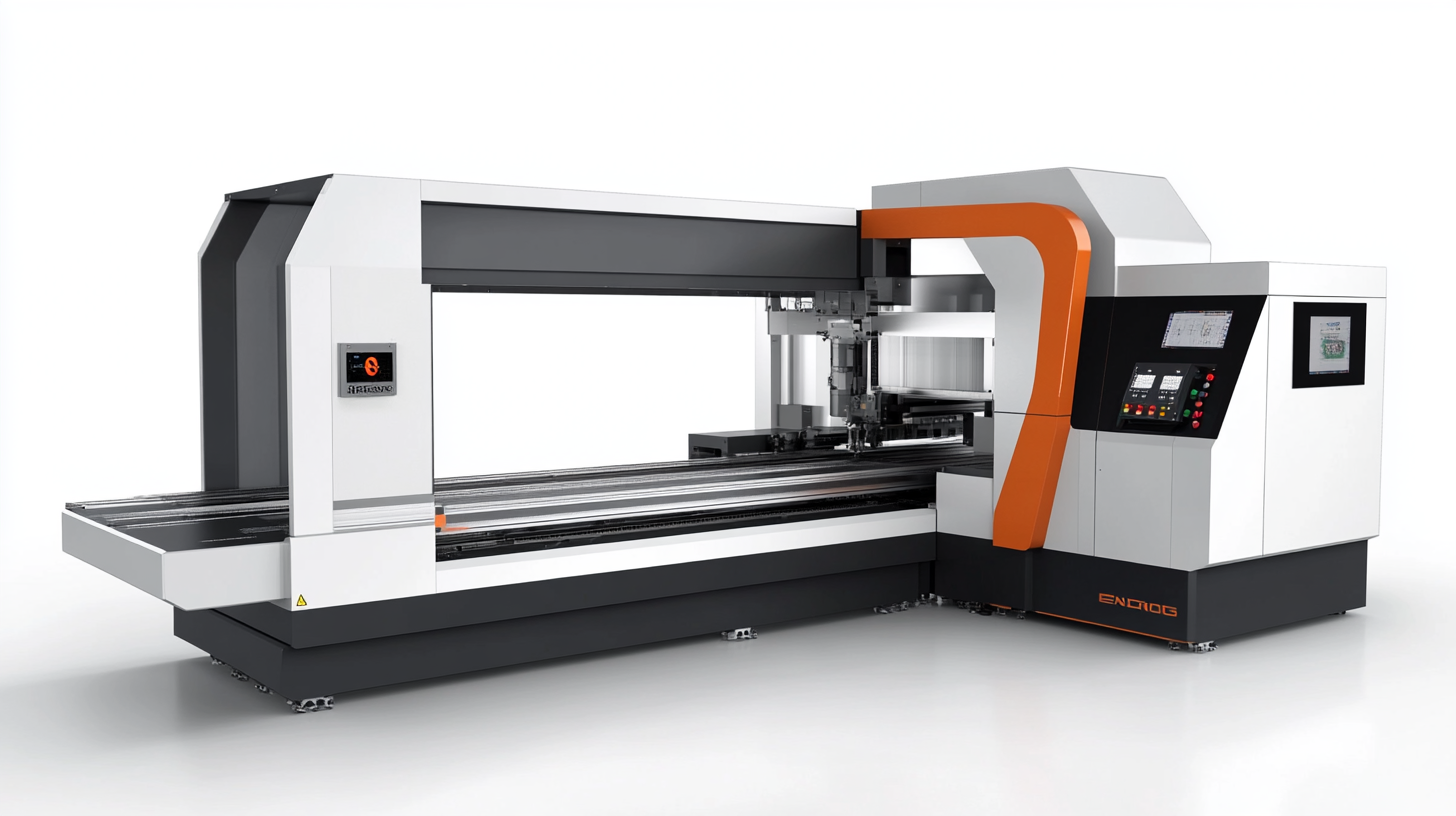
The Role of Software Innovations in Enhancing CNC Cutting Precision
Software innovations play an increasingly important role in CNC cutting technology. Advanced software tools allow real-time monitoring and adjustments during cutting processes, which can result in better accuracy and improved quality control. According to MarketsandMarkets recently published report, "CNC software is expected to reach $6.86 billion by 2026 at a CAGR of 8.5% from 2021," at a continued rise towards software-centric CNC solutions during the next few years.
The innovation of simulation software has mainly transformed the manufacturing industry, allowing manufacturers to visualize and improve cutting processes without actual fabrication. Using advanced algorithms and artificial intelligence, these tools study the performance of machines and predict problems, leading to minimized material waste and defects. As reported by the International Journal of Advanced Manufacturing Technology, companies that utilize simulation software report up to 30% improvement in efficiencies and tricks on these technologies.
Moreover, user-friendly interfaces and cloud-based solutions are being made more common by these greater learnings to smaller manufacturers. The development in technology has thereby begun to make available the latest software to all global buyers without spending heavily on training or infrastructure for productive use, thus enhancing competitiveness in the market. Therefore, with the expansion of software capabilities, CNC cutting is likely to gain considerably in terms of better precision and operational efficiency.
Best Practices for Selecting the Right CNC Cutting Equipment Worldwide
It's essential to get informed about purchasing decisions because global importers of CNC cutting machines will have multiple very different ones choosing from two that will greatly weigh on both their production efficiency and precision. According to that has emerged on the subject from MarketsandMarkets-Its global CNC machine market estimates say it could grow to exceed $117 billion by 2026 from $80 billion in just 2021. These conditions make it imperative that clear and objective specifications are understood in terms of specific production needs.
Best practice when it comes to buying CNC cutting equipment is to scrutinize machine performance in terms of precision and material compatibility. For instance, machines capable of high speed spindle and adaptive feed control functions dramatically increase cutting precision, hence making them most suited to aluminum and titanium types. A survey conducted by The Fabricator revealed that 67% of manufacturers consider precision features first when spending on CNC equipment, necessitating alignment of technical specs with operational objectives.
That's why assessing the training and after-sales support for machines from the manufacturers is very important. It noted that those organizations increased their productivity operation efficiency by 25% by having strong training programs about their equipment. As most buyer navigates through a huge maze of CNC technology, support for the equipment in terms of service will give it all-encompassing benefits like reduced downtime and production efficiency in the long run. Thus, these best practices can help global buyers make informed decisions that optimize their CNC cutting operations.
NORTH EASTON MACHINE • 218 Elm Street • North Easton, MA 02356 • 508-238-6219