How to Identify Top Tier Precision CNC Machining Suppliers for Your Manufacturing Needs
In today's competitive manufacturing landscape, identifying top-tier precision CNC machining suppliers is crucial for ensuring product quality and operational efficiency. According to the ReportLinker Global CNC Machining Market report, the CNC machining industry is projected to surpass $105 billion by 2026, driven by its increasing application across several sectors, including automotive, aerospace, and medical devices. The precision CNC machining process, characterized by its ability to produce complex and intricate parts with extreme accuracy, is setting a new standard for manufacturing excellence.
As manufacturers strive to enhance their competitive edge, selecting a reliable precision CNC machining supplier becomes a paramount decision. Industry studies indicate that organizations partnering with high-quality suppliers can reduce production costs by up to 30% while achieving superior product performance. Therefore, understanding the key factors for identifying top-tier precision CNC machining suppliers is essential for businesses aiming to optimize their manufacturing processes and leverage cutting-edge technology for optimum results.
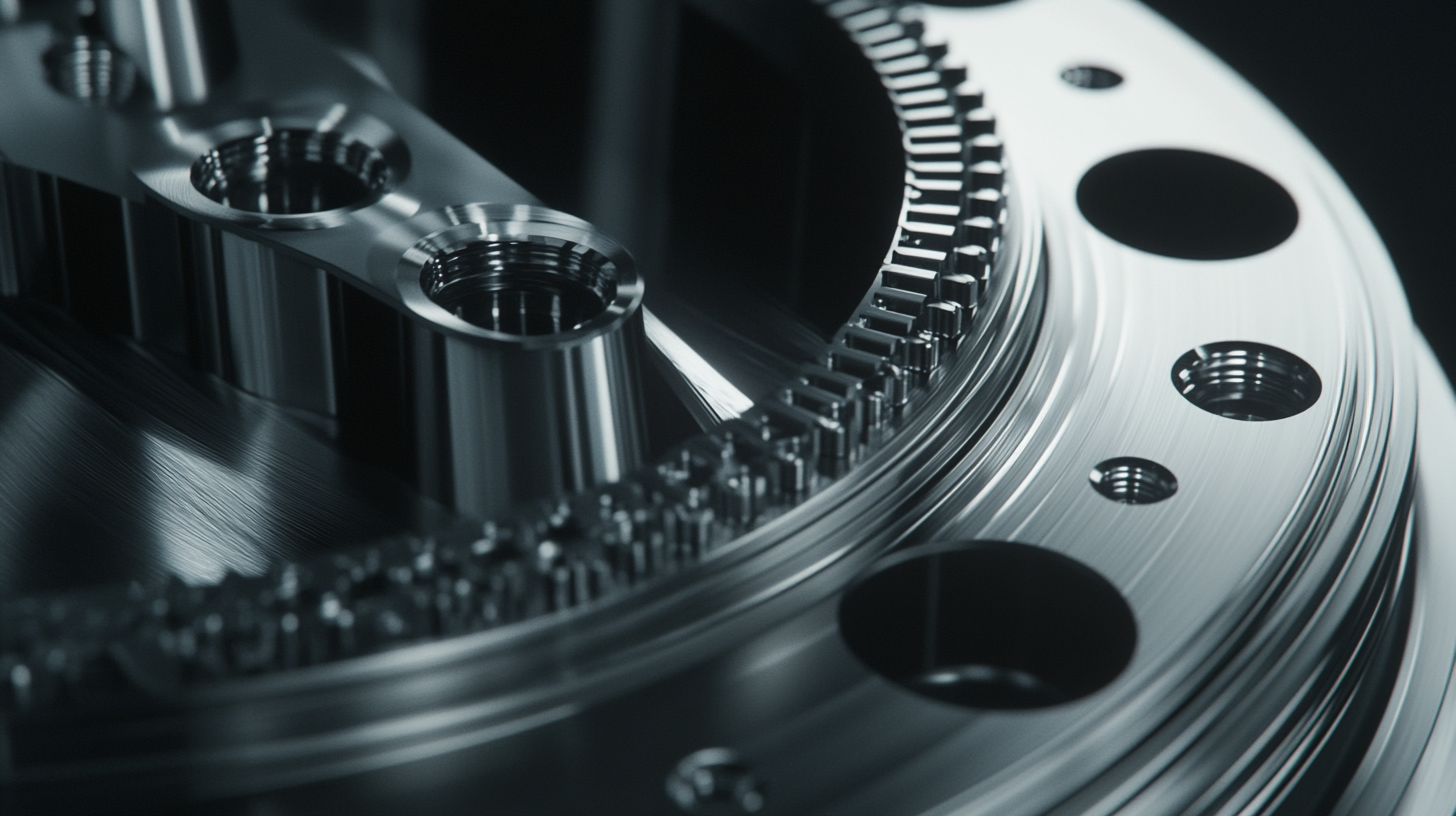
Key Attributes of Top Tier CNC Machining Suppliers to Consider
When seeking top-tier CNC machining suppliers, it's essential to consider key attributes that can significantly impact your manufacturing needs. One of the foremost characteristics is their adaptability to technology, particularly in incorporating Artificial Intelligence (AI) into their processes. AI is revolutionizing manufacturing by enhancing efficiency and precision, enabling suppliers to optimize production and minimize errors. Suppliers who leverage AI can respond quickly to changing market demands and improve overall product quality, making them invaluable partners for your business. Another crucial attribute is the supplier's commitment to analytical thinking. As businesses increasingly prioritize data-driven decision-making, a supplier's ability to analyze trends, production metrics, and performance indicators becomes vital. This skill set not only aids suppliers in improving their own operations but also empowers them to offer insightful recommendations to their clients, enhancing collaboration and efficiency in the manufacturing process. Furthermore, a strong emphasis on automation and advanced machinery is essential. Modern CNC machining companies should demonstrate a keen understanding of the latest technological advancements, enabling them to maintain competitiveness in a rapidly evolving market. By investing in high-quality machinery and maintaining rigorous quality control standards, they ensure that they can meet precise specifications while managing production costs effectively. The combination of these attributes positions top-tier CNC machining suppliers as strategic partners in driving your manufacturing success.
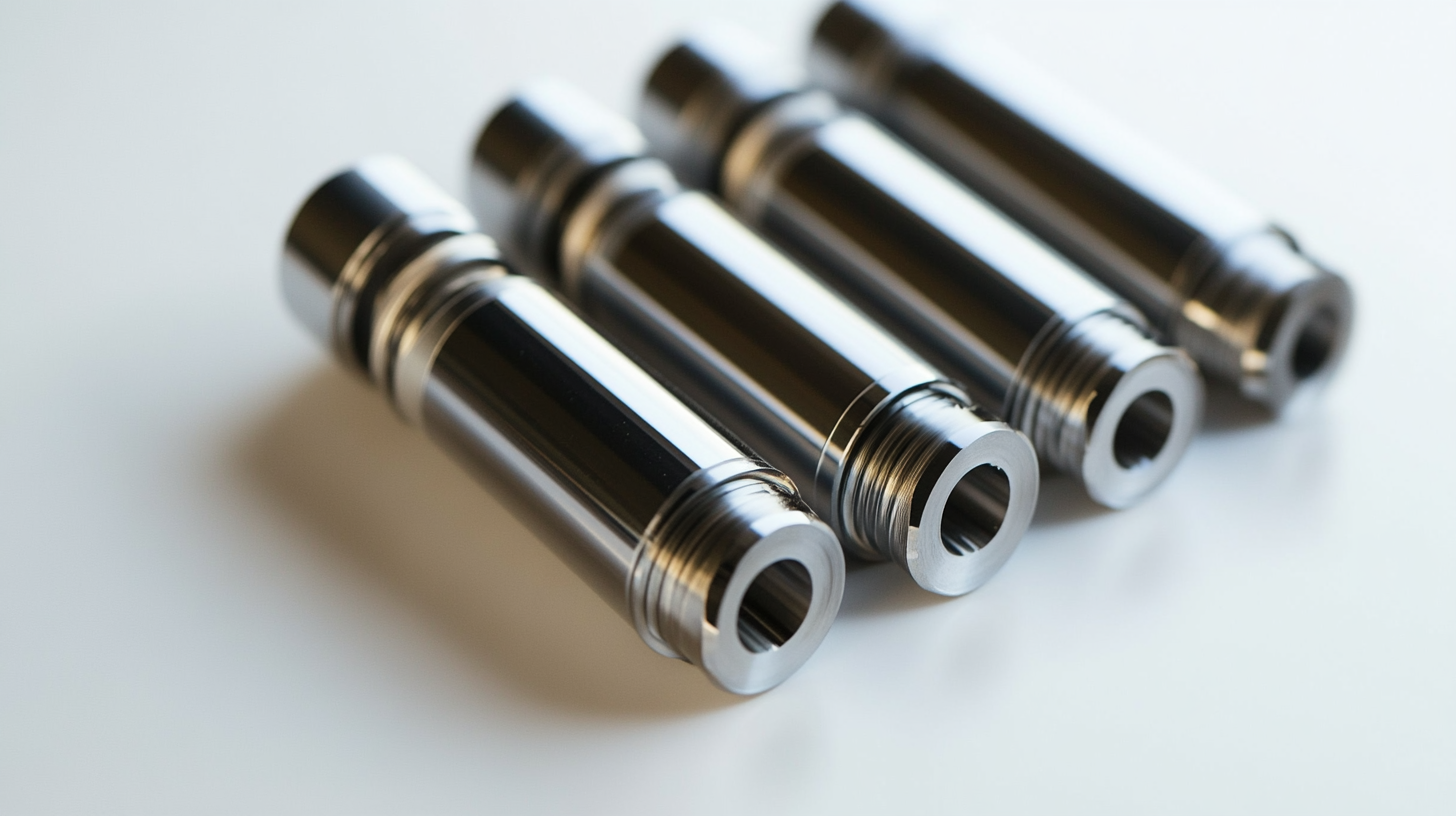
Evaluating Supplier Credentials: Certifications and Industry Experience
When evaluating CNC machining suppliers, understanding their credentials is paramount. Certifications serve as a standardized measure of quality, ensuring that the suppliers adhere to industry-specific regulations and practices. For instance, certifications such as ISO 9001 can provide assurance regarding a supplier's quality management systems. Additionally, suppliers with industry-recognized credentials boast a higher degree of accountability, reflecting their commitment to maintaining high production standards.
Industry experience is another critical factor in this evaluation process. Suppliers with extensive experience in the CNC machining field often possess deeper insights into industry trends, advanced technologies, and optimal practices. Such expertise not only boosts confidence in their capabilities but also aids in anticipating and addressing challenges that may arise during the manufacturing process. Collaborating with seasoned suppliers can facilitate smoother project execution, contributing to higher efficiency and reduced overhead costs.
Moreover, the ability to manage risk effectively is now a significant aspect of supplier evaluation. With today's complex supply chains, companies must prioritize suppliers who demonstrate robust risk management practices. Utilizing analytical tools and platforms that monitor supplier performance and compliance can help manufacturers maintain an edge in the competitive landscape. By aligning with top-tier CNC machining suppliers who excel in credential verification and possess substantial industry experience, manufacturers can secure a reliable foundation for their production needs.
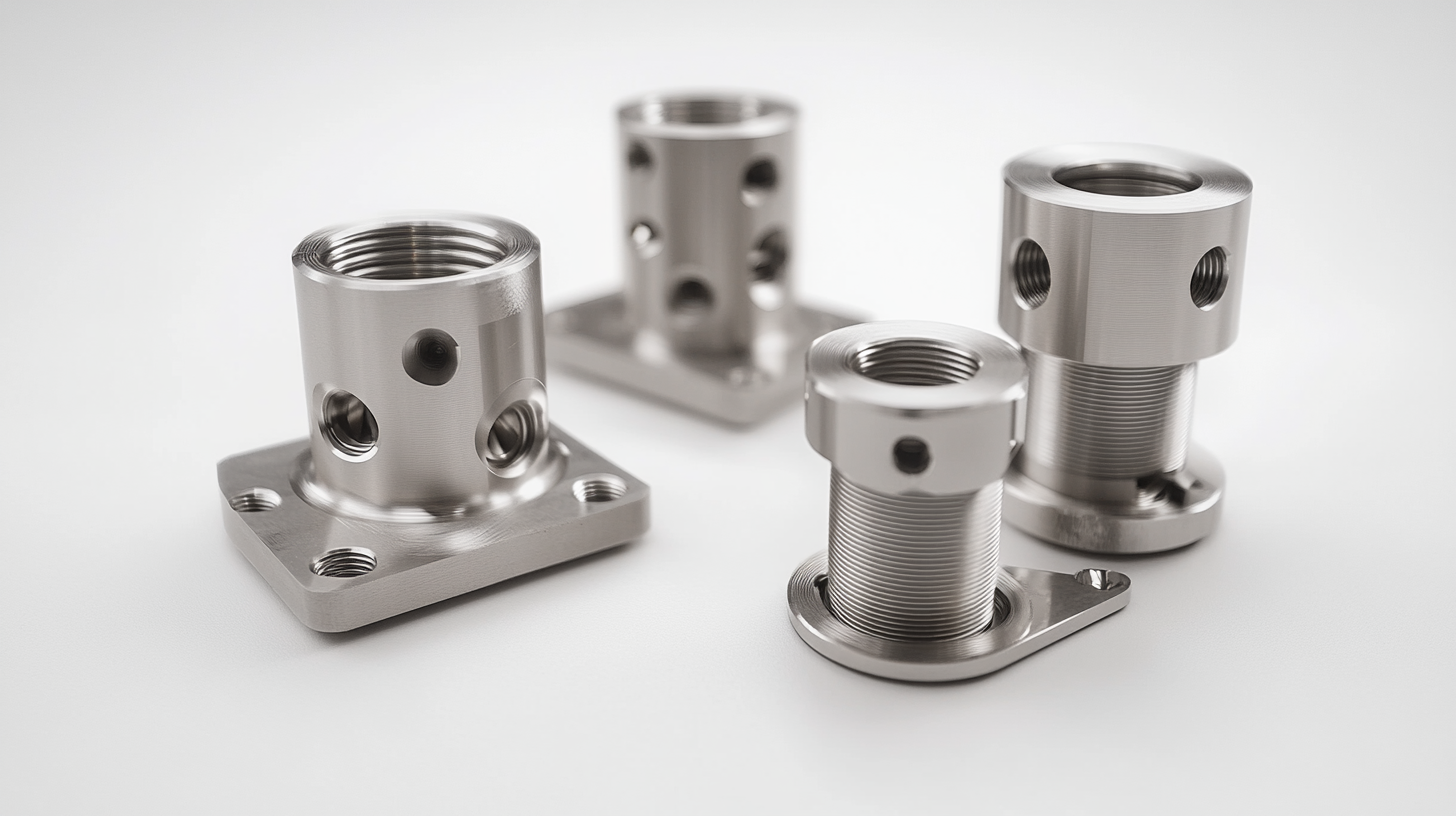
Understanding Our Equipment and Capabilities: A Vital Criterion
When searching for top-tier precision CNC machining suppliers, understanding their equipment and capabilities is crucial. The machinery used in a CNC shop not only determines the accuracy and quality of the parts produced but also affects turnaround time and cost efficiency. Suppliers that invest in state-of-the-art machinery, such as multi-axis CNC mills and lathes, can offer greater precision and the ability to handle complex geometries. This investment often reflects a commitment to high standards and innovation that can benefit your manufacturing needs.
Additionally, a supplier's capabilities should extend beyond their equipment. It’s essential to consider their expertise in different materials and the range of services offered, such as prototyping, finishing, and assembly. A company that excels in a variety of materials—metals, plastics, composites—demonstrates versatility and the ability to meet diverse project requirements. Furthermore, examining their quality control processes will reveal how they ensure consistency and adherence to specifications, which is vital for maintaining industry standards.
Ultimately, understanding the alignment between your project requirements and a supplier's capabilities can significantly impact the success of your manufacturing endeavors. Engaging in discussions about their equipment and experience will not only provide insight into their operational strengths but will also help build a collaborative relationship that fosters innovation and efficiency in your production processes.
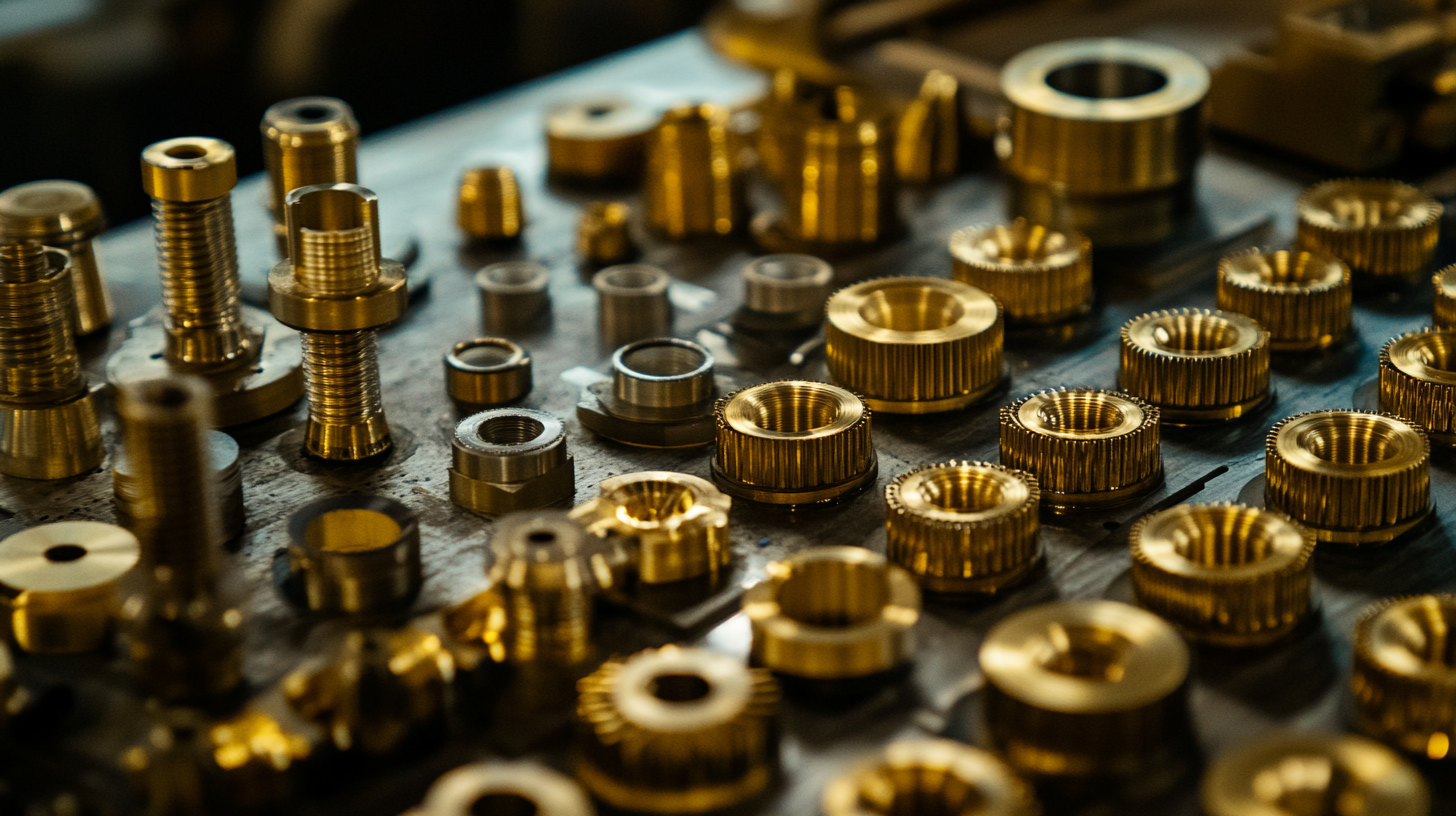
Assessing Communication and Support Services for Manufacturing Projects
In today’s competitive manufacturing landscape, selecting the right precision CNC machining supplier hinges not just on technical capabilities but significantly on communication and support services. Effective communication acts as a cornerstone for successful collaboration, ensuring that project requirements are clearly understood and addressed. Suppliers who prioritize clear, ongoing dialogue help alleviate potential missteps in production, thereby enhancing overall project outcomes.
Furthermore, support services play a vital role in this equation. A top-tier supplier should provide not just immediate assistance but also strategic insights throughout the manufacturing process. This includes regular updates, responsiveness to inquiries, and proactive solutions to any challenges that may arise. As industries increasingly embrace digital engineering and data-driven solutions, the integration of advanced communication tools tailored for collaborative projects becomes imperative. These tools can streamline interactions, facilitate better information sharing, and foster a more integrated approach to project management.
Amid a shifting regulatory landscape and evolving industry demands, the adaptability of suppliers is crucial. Those who invest in robust communication infrastructures and support frameworks are better positioned to respond to the complexities of modern manufacturing. This proactive approach not only addresses immediate operational needs but also builds resilience against future challenges, ensuring that both manufacturers and CNC machining suppliers can thrive together in a rapidly changing environment.
Pricing Strategies: Balancing Cost and Quality in CNC Machining Services
When it comes to selecting a CNC machining supplier, understanding pricing strategies is crucial for balancing cost and quality. Many manufacturers often find themselves tempted to choose the lowest-priced option, but this can lead to compromises in the quality of the finished product. Effective pricing strategies involve a comprehensive evaluation of not only the cost but also the value that each supplier can bring to the table.
One effective approach is to consider pricing tiers based on the complexity of machining projects. High-precision components may require more advanced technology and skilled labor, which understandably come at a higher price. However, these investments often result in increased durability and performance, reducing long-term costs associated with repairs and rework. Manufacturers should assess the specific requirements of their projects and determine if the higher upfront costs will yield better overall results.
Moreover, transparency in pricing is a key factor when negotiating with CNC machining suppliers. Understanding the breakdown of costs—such as material expenses, labor fees, and overhead—allows manufacturers to make informed decisions. Suppliers who provide detailed quotes and options for cost-saving measures, like bulk order discounts or alternative materials, can facilitate a more beneficial partnership. Ultimately, a well-considered pricing strategy that recognizes the balance between cost and quality can pave the way for successful manufacturing outcomes.
NORTH EASTON MACHINE • 218 Elm Street • North Easton, MA 02356 • 508-238-6219