Navigating the Future: Essential Insights into Multi Axis CNC Milling Machine Procurement
In recent years, the manufacturing landscape has witnessed a significant transformation driven by advancements in technology and automation. The rise of precision engineering has propelled the demand for sophisticated machinery, particularly the Multi Axis CNC Milling Machine. According to a report by MarketsandMarkets, the global CNC machines market is projected to reach USD 100 billion by 2025, with Multi Axis CNC Milling Machines playing a pivotal role in this growth due to their ability to enhance efficiency, accuracy, and versatility in complex fabrication processes.
As industries seek to improve production capabilities and reduce operational costs, the procurement of Multi Axis CNC Milling Machines has become a strategic consideration for manufacturers. The enhanced capabilities of these machines, such as the ability to perform multiple tasks in a single setup and their adaptability for intricate designs, underscore their significance in modern manufacturing. Furthermore, a study by Grand View Research highlights that the increasing adoption of smart manufacturing technologies will further catalyze the demand for these machines, making it imperative for organizations to navigate procurement wisely to leverage their potential and stay competitive in the evolving market.
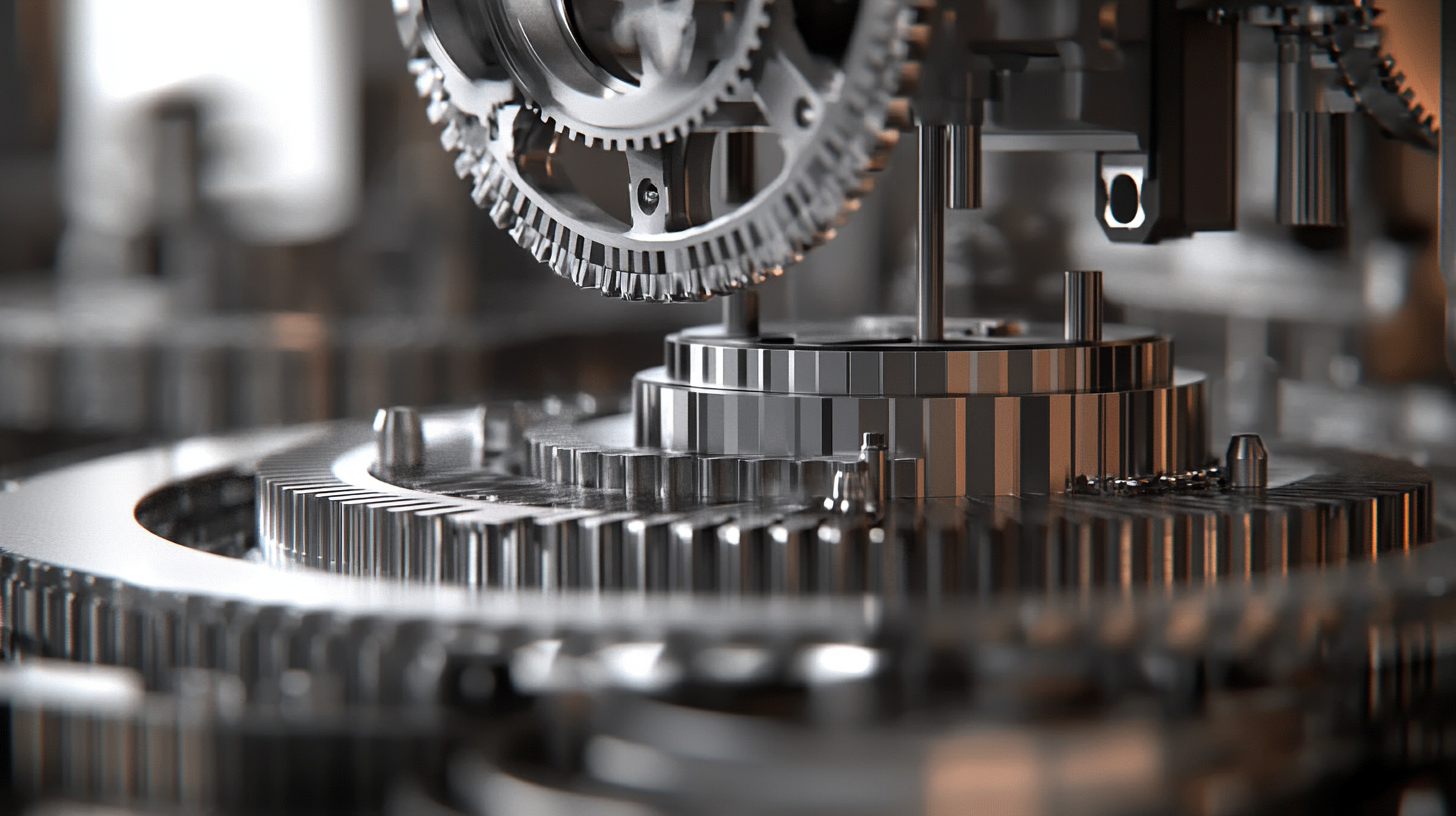
Understanding the Basics of Multi Axis CNC Milling Machines
When it comes to multi-axis CNC milling machines, understanding the basics is crucial for any procurement process. Multi-axis machining refers to the ability of a CNC machine to move the cutting tool or workpiece along multiple axes simultaneously. Typically, this includes 3-axis, 4-axis, and 5-axis systems, with 5-axis machines allowing for more complex geometries and improved efficiency. This versatility not only enhances production time but also opens the door to intricate designs that would be challenging to achieve with traditional machining methods. A key aspect of multi-axis CNC milling is the concept of kinematic transformations. This refers to the adjustments made to the machine to maintain accurate tool orientation throughout the milling process. For instance, when employing 5-axis milling, operators must ensure precise configuration and simulation before beginning operations to prevent potential crashes. The knowledge of these kinematic transformations enhances the operator’s capacity to optimize tool paths and improve machining accuracy, ultimately leading to better product quality. Moreover, the integration of advanced technological solutions, such as dynamic machining techniques, emphasizes the ongoing evolution in the field. Innovations in tool positioning and orientation techniques are continually reshaping how multi-axis machines operate, enhancing productivity and precision in manufacturing environments. By grasping these foundational concepts, operators can make informed decisions regarding machine procurement, ensuring that their investments align with their production goals and operational requirements.
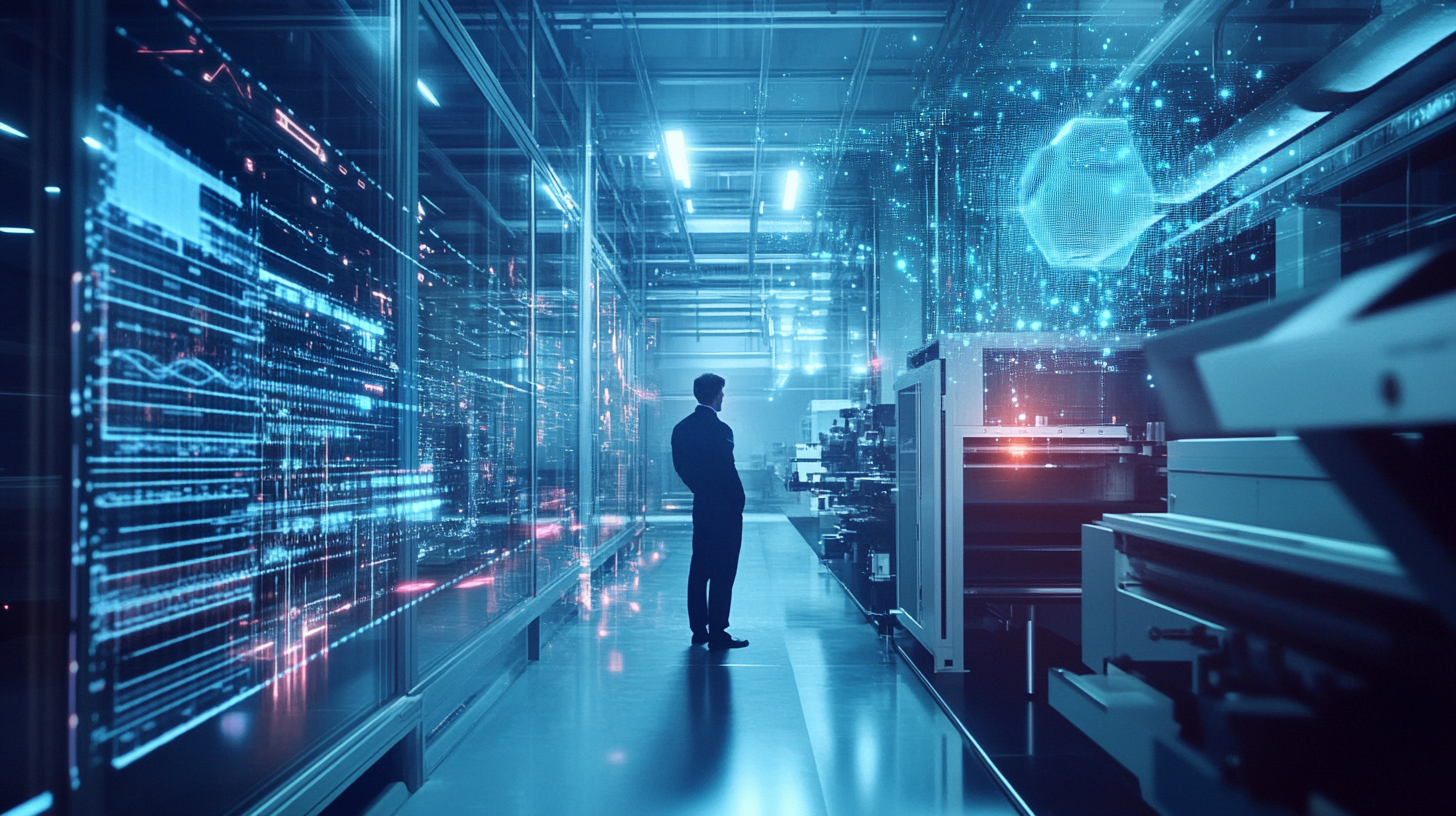
Key Factors to Consider When Sourcing CNC Milling Equipment
When sourcing CNC milling equipment, particularly multi-axis CNC milling machines, several key factors should be meticulously considered to ensure optimal performance and return on investment. The global CNC machining market is projected to grow significantly, with estimates indicating it could reach $100 billion by 2025, reflecting a CAGR of about 6.2% from 2020. This growth underscores the importance of choosing the right CNC milling machines that align with market trends and industry demands.
One of the most critical considerations is the machine's precision and accuracy. In sectors such as aerospace and automotive, tolerances can be as tight as ±0.005 mm, and investing in a machine that meets or exceeds these specifications is vital for maintaining competitive edge. Additionally, the versatility of multi-axis machines allows for complex geometries to be produced in a single setup, reducing cycle time and improving overall efficiency, which is particularly valued in high-demand environments.
Another essential factor is the technological features of the CNC milling machines, such as CNC software compatibility and ease of programming. According to a recent report, machines equipped with advanced features such as adaptive machining and real-time monitoring can significantly enhance operational efficiency. Organizations seeking to optimize their production lines will benefit from machines that not only meet current needs but are also scalable for future technological advancements.
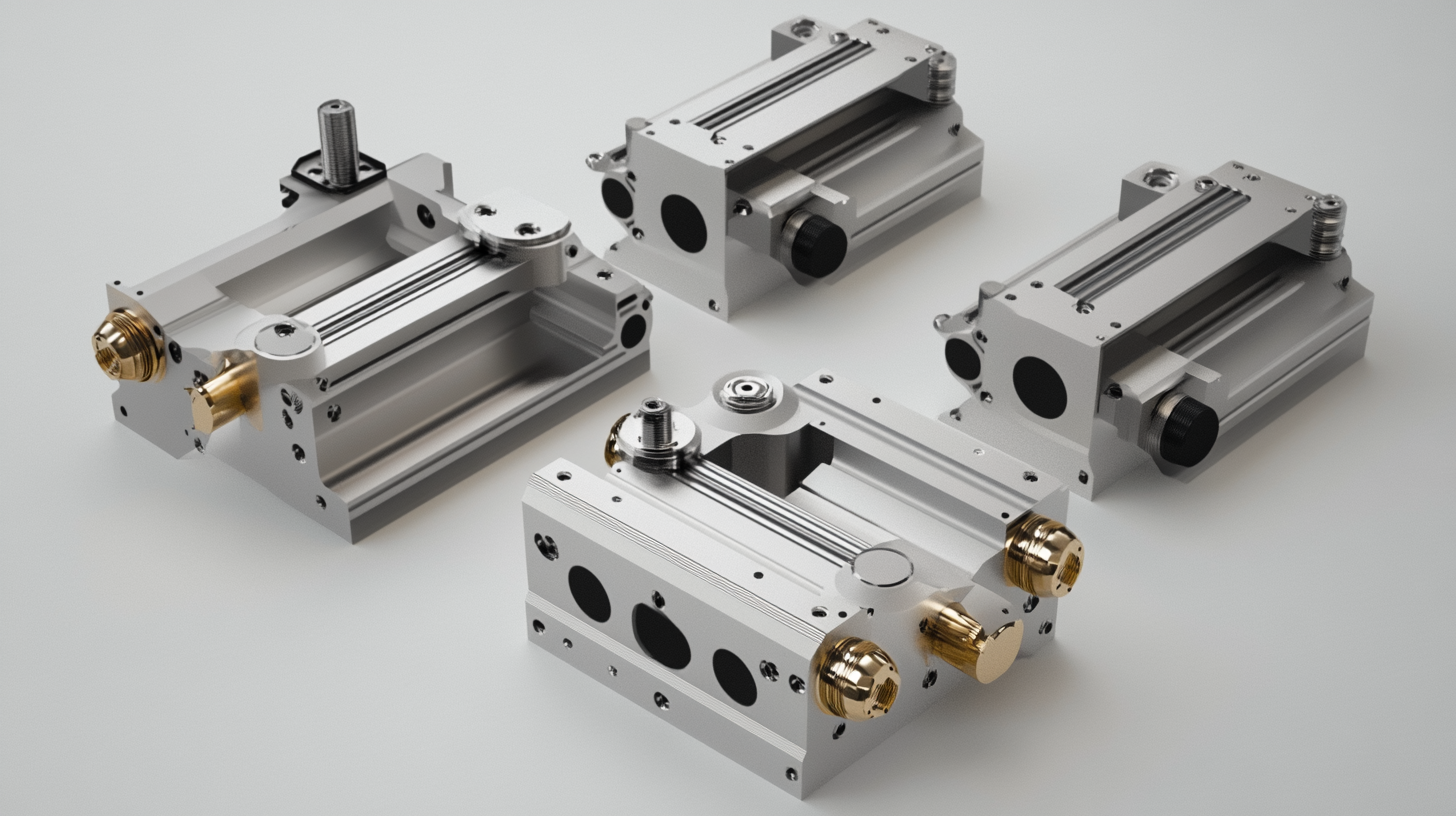
Evaluating Supplier Reliability and Support Services
In the realm of multi-axis CNC milling machine procurement, supplier reliability and support services play a pivotal role in ensuring successful integrations and operational efficiency. As manufacturers ramp up production capabilities, the quest for dependable suppliers becomes even more critical. According to a recent report from the Association for Manufacturing Technology, nearly 70% of manufacturers cite supply chain reliability as a primary concern affecting their production schedules. Having a robust framework for evaluating suppliers is essential; this involves assessing their experience, industry reputation, and the quality of after-sales service they provide.
Moreover, the evolution of sourcing platforms has greatly transformed the procurement landscape. Oil and gas companies, for instance, can learn from the features touted in recent sourcing platform insights, such as enhanced data analytics, supplier performance scoring, and seamless communication channels. Implementing these features can significantly streamline the procurement process for CNC machinery, enabling stakeholders to make informed decisions swiftly. A study from the Procurement Leaders Network indicates that incorporating advanced sourcing solutions can enhance procurement efficiency by up to 40%, allowing manufacturers to allocate resources toward innovation rather than operational bottlenecks.
Ultimately, the journey of procuring a multi-axis CNC milling machine requires a strategic approach, particularly in assessing supplier reliability and their support services. This proactive evaluation not only mitigates risks associated with machine downtime but also ensures alignment with long-term production goals. As the manufacturing landscape evolves, investing time and resources into supplier assessment practices will be crucial for sustained operational success.
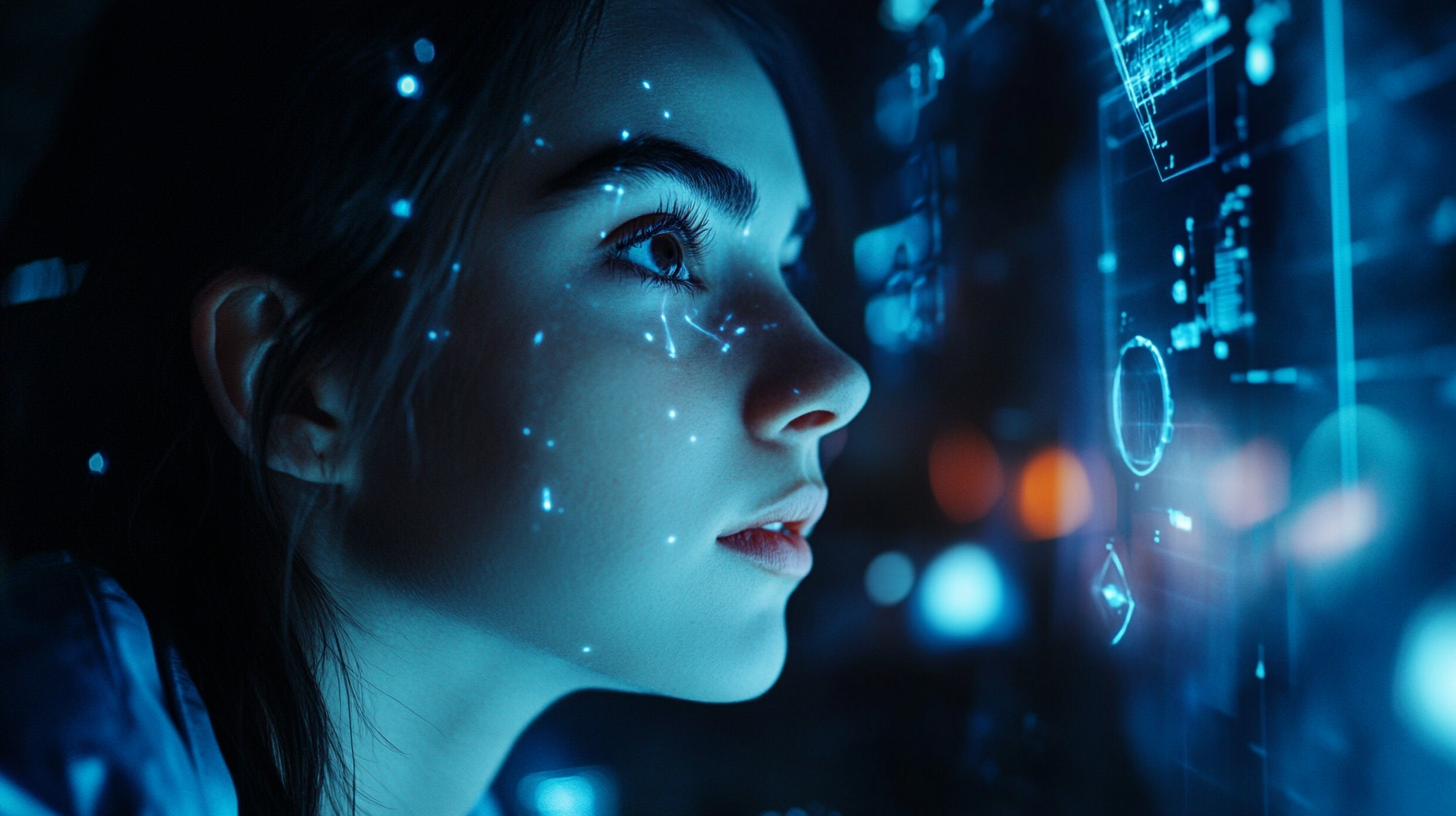
Budgeting for Multi Axis CNC Milling Machine Procurement
When considering the procurement of multi-axis CNC milling machines, budgeting is a critical factor that can significantly impact project success and overall efficiency. Recent industry reports indicate that the global CNC milling machine market is projected to reach USD 100 billion by 2025, with a compound annual growth rate (CAGR) of around 5.2%. This robust growth underscores the importance of strategic budgeting in capitalizing on technological advancements that these machines offer.
To effectively budget for a multi-axis CNC milling machine, businesses should first evaluate the total cost of ownership (TCO). This includes not only the initial purchase price, which can range from USD 50,000 to over USD 500,000 depending on the machine's capabilities, but also ongoing expenses such as maintenance, tooling, and software updates. According to a study by Technavio, nearly 30% of budget overruns are attributed to unplanned operational costs. Therefore, incorporating these elements into the financial plan can help avoid surprises down the line.
Additionally, companies should consider the return on investment (ROI) associated with acquiring advanced milling technology. Reports from Frost & Sullivan emphasize that integrating multi-axis machines can increase productivity by up to 30% and reduce machining time by up to 50%. Businesses that engage in detailed market research and seek competitive quotes are better positioned to secure advantageous financing options, which can further ease the budgeting process while ensuring that they invest in solutions that align with their long-term operational goals.
Future Trends in CNC Milling Technology and Their Impact
The realm of CNC milling technology is transforming at an unprecedented pace, driven by advancements in automation, artificial intelligence, and material science. According to a recent market report by Grand View Research, the global CNC machine market is expected to reach $117.93 billion by 2028, growing at a compound annual growth rate (CAGR) of 6.5%. This rapid growth underscores the increasing reliance on CNC milling machines across various industries, including aerospace, automotive, and medical, where precision and efficiency are paramount.
Future trends indicate that the integration of IoT and machine learning will significantly enhance the capabilities of multi-axis CNC milling machines. By utilizing real-time data analytics, manufacturers can optimize machine performance, predictive maintenance schedules, and quality control processes. A study conducted by MarketsandMarkets projects that the IoT in manufacturing market will reach $398.85 billion by 2025, presenting a tremendous opportunity for CNC technologies to evolve and adapt in this connected ecosystem.
Additionally, the demand for advanced materials such as titanium and carbon fiber composites is escalating. As reported by Mordor Intelligence, the global market for advanced composite materials is anticipated to grow at a CAGR of 9.4% from 2020 to 2025. This trend necessitates the development of specialized multi-axis CNC machines capable of handling these tough materials, thereby enhancing machining efficiency and product performance.
In summary, staying abreast of these trends is crucial for companies aiming to invest in CNC milling technology. Adopting cutting-edge systems that incorporate AI, IoT, and advancements in materials will not only improve operational efficiency but also position businesses competitively in an evolving marketplace.
NORTH EASTON MACHINE • 218 Elm Street • North Easton, MA 02356 • 508-238-6219