The Evolution of Cnc Machining Parts in Global Manufacturing
The landscape of global manufacturing has undergone significant transformation over the past few decades, driven by technological advancements and market demands. Among these innovations, CNC machining parts have emerged as a pivotal component, revolutionizing production processes and enhancing precision. CNC, or Computer Numerical Control, enables manufacturers to produce intricate components with unparalleled accuracy, efficiency, and repeatability. As industries continue to evolve, the role of CNC machining parts becomes increasingly vital, impacting everything from automotive to aerospace and beyond.
This blog delves into the evolution of CNC machining parts, tracing their development and the impact they have had on manufacturing practices worldwide. We will explore the various technologies that have emerged, the improvements in material science, and how automation is reshaping production lines. Understanding the journey of CNC machining parts not only highlights their importance in contemporary manufacturing but also sets the stage for innovations that lie ahead. Join us as we uncover the critical role these components play in shaping the future of global manufacturing.
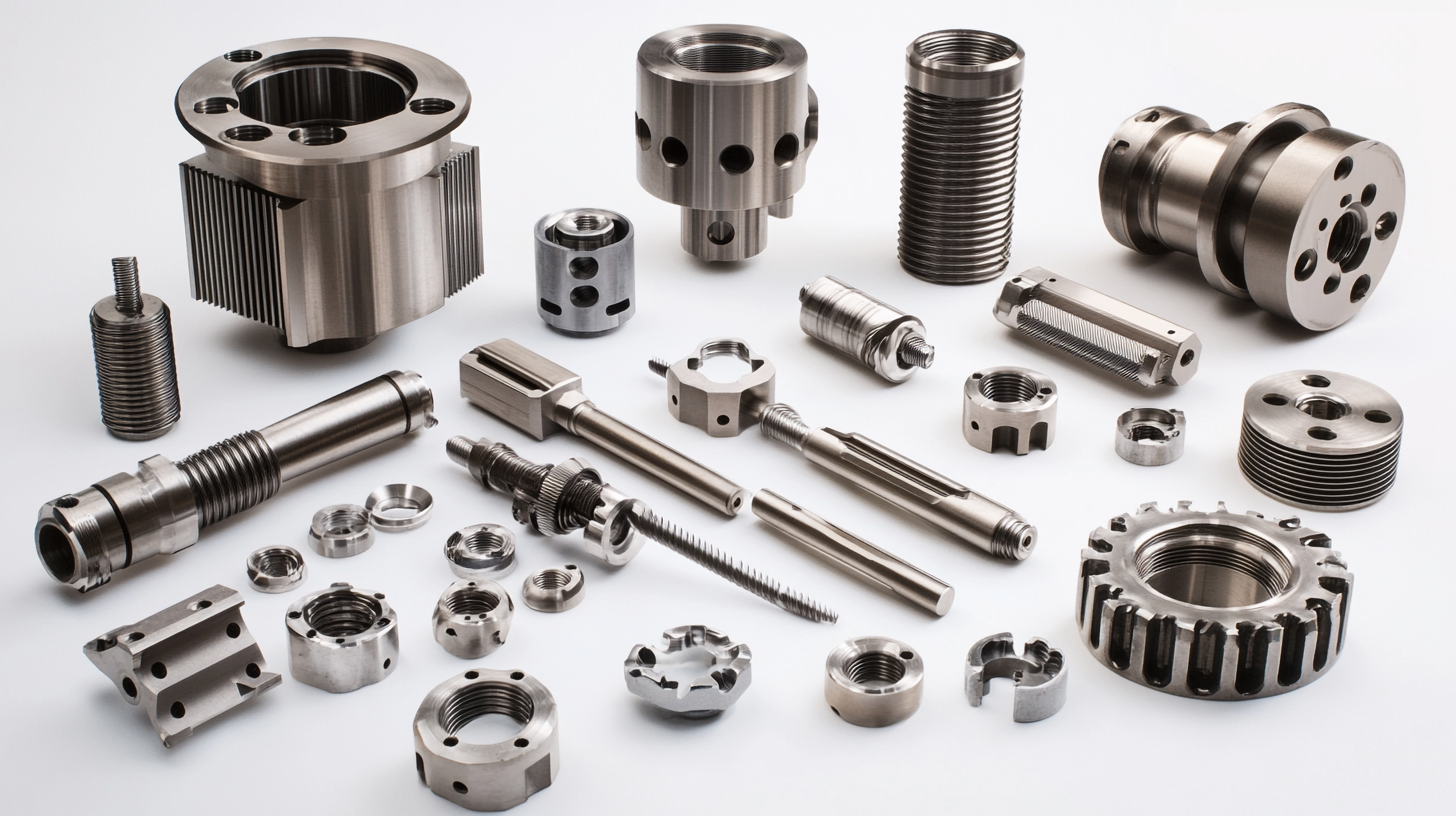
The Historical Background of CNC Machining in Manufacturing
CNC machining has transformed the landscape of global manufacturing since its inception in the mid-20th century. With the advent of computer numerical control technology, the precision and repeatability of machining processes improved drastically, allowing manufacturers to produce complex parts with minimal human intervention. According to a 2021 industry report, the CNC machining market was valued at approximately $70 billion, demonstrating its critical role in various sectors, including aerospace, automotive, and electronics.
The historical trajectory of CNC machining underscores its evolution from conventional machining methods to today's sophisticated automated systems. Initially, the process relied heavily on operator skill and manual controls, limiting production capabilities. However, advancements in computer technology and software integration have enabled manufacturers to optimize workflows, reduce lead times, and enhance product quality. Notably, a study by a leading market research firm highlighted that companies utilizing CNC machining saw a productivity increase of up to 30% compared to traditional methods.
As we examine CNC's legacy, it becomes evident that other emerging technologies, such as 3D printing, can benefit from its historical lessons. The ability to adapt, innovate, and streamline processes has been a hallmark of CNC machining's success. With the 3D printing industry still in its formative years, embracing these principles could pave the way for remarkable advancements, ensuring that it does not join the ranks of obsolete manufacturing tools but rather evolves alongside them in the competitive landscape.
Key Technological Advancements in CNC Machining Parts
The field of CNC machining has seen remarkable advancements over the past few decades, driven by the rapid integration of technology into global manufacturing. One significant technological leap is the development of advanced computer-aided design (CAD) and computer-aided manufacturing (CAM) systems. According to a report from Grand View Research, the global CAD market size was valued at USD 9.8 billion in 2020, and it is expected to grow at a compound annual growth rate (CAGR) of 7.2% from 2021 to 2028. This growth enhances design efficiency and precision in CNC machining parts, enabling manufacturers to produce complex geometries with higher fidelity.
Another key advancement lies in the emergence of additive manufacturing (AM) techniques, which have increasingly been integrated with traditional CNC machining. The Wohlers Report indicates that the additive manufacturing industry saw a significant increase, growing by 7.5% in 2019 to reach USD 11.58 billion. By combining CNC machining with additive processes, manufacturers can optimize material usage and reduce waste, leading to more sustainable production practices. This synergy not only improves product performance but also accelerates the prototyping phase, allowing for quicker iteration and innovation.
Moreover, the incorporation of artificial intelligence (AI) into CNC machining workflows is transforming how manufacturers approach production. AI technologies enable predictive maintenance and enhanced operational efficiencies. A study by McKinsey suggests that by adopting AI, manufacturers could increase productivity by up to 20%, showcasing its potential to revolutionize CNC machining operations. These advancements reflect a broader trend where technology fosters greater agility, precision, and sustainability in the manufacturing landscape, underscoring the evolution of CNC machining parts on a global scale.
Impact of CNC Machining on Production Efficiency and Accuracy
The impact of CNC machining on production efficiency and accuracy cannot be overstated in the context of modern manufacturing. With the ongoing advancements in technology, enterprises worldwide are increasingly turning to CNC machines to streamline their operations. The rise of automation has facilitated an environment where precision and efficiency are paramount, allowing manufacturers to produce complex parts with a high degree of accuracy and minimal waste. In fact, market reports indicate that the global CNC market is poised for significant growth, driven by the demand for innovative manufacturing solutions that embrace efficiency and provide consistent results.
Recent trends suggest that the integration of AI and data analytics within CNC machining operations is ushering in a new era of manufacturing. AI technologies are transforming how machines operate, enabling self-optimized cutting processes that not only enhance precision but also significantly reduce production times. This shift is evident in the growing market for advanced 5-axis CNC machining centers, which are projected to see substantial growth in the coming years. Such technologies embody the essence of smart manufacturing, where real-time feedback and machine learning algorithms contribute to an overall increase in productivity and reduction in errors.
Furthermore, the emergence of Industry 4.0 principles, including comprehensive feedback loops and digital connectivity, is revolutionizing precision engineering. The application of big data in metrology ensures that production processes are continuously monitored and adjusted, leading to unprecedented levels of quality control. As manufacturers continue to embrace these transformative technologies, the efficiency and accuracy achieved through CNC machining will play a pivotal role in meeting the ever-growing demands of various industries.
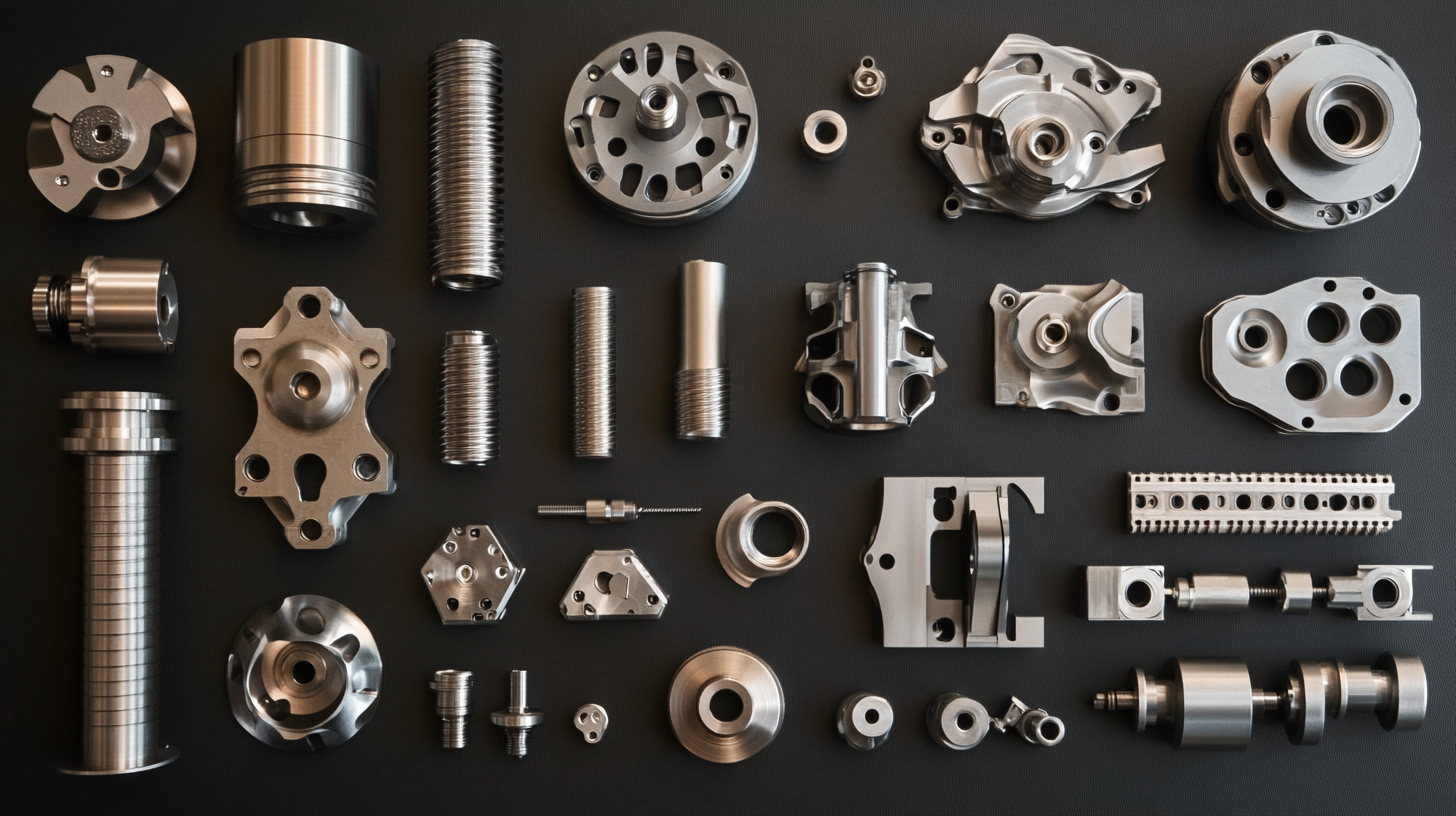
Global Trends Shaping the Future of CNC Machining Parts
The landscape of CNC (Computer Numerical Control) machining parts in global manufacturing is undergoing transformative changes that reflect broader industry trends. According to a recent report by Market Research Future, the global CNC machining market is expected to grow at a compound annual growth rate (CAGR) of 6% from 2021 to 2027. This growth is driven by technological advancements and increasing demand for precision in manufacturing processes.
One of the most significant trends impacting CNC machining parts is the integration of automation and Industry 4.0 technologies. With the rise of smart factories, manufacturers are increasingly adopting IoT-enabled CNC machines that enhance operational efficiency and provide real-time data analytics. A study from Deloitte highlights that 80% of manufacturers are investing in automation technologies to improve productivity and reduce lead times. This shift not only maximizes production capabilities but also allows for greater customization and flexibility in manufacturing processes.
Sustainability is another pivotal trend shaping the future of CNC machining. With rising concerns over environmental impacts, manufacturers are seeking greener practices by implementing energy-efficient CNC systems and utilizing eco-friendly materials. The International Federation of Robotics reported that adopting such technologies could reduce energy consumption in manufacturing by up to 30%. As businesses aim for sustainable growth, the demand for CNC machined parts that adhere to environmental standards is expected to rise significantly, confirming that ecological responsibility is becoming a key driver in the industry.
Sustainability and Environmental Considerations in CNC Machining
The manufacturing sector is undergoing a significant transformation, with sustainability becoming a focal point in the production processes, particularly in CNC (Computer Numerical Control) machining. This technology, essential for creating precision parts, can significantly impact environmental sustainability. The shift towards greener practices means that manufacturers now prioritize the use of eco-friendly materials, energy-efficient machines, and waste minimization strategies.
One of the key ways CNC machining contributes to sustainability is through its ability to optimize material usage. Advanced software algorithms allow for precise calculations in the cutting process, reducing scrap rates and ensuring that every piece of material is utilized efficiently. Additionally, manufacturers are increasingly adopting recyclable materials in their machining processes, thereby minimizing the ecological footprint associated with producing and disposing of conventional materials.
Moreover, the energy consumption of CNC machines is under scrutiny. Innovators are developing machines that not only consume less power but also employ regenerative technologies, which recover energy during the machining process. This transition to energy-efficient systems not only lowers operational costs but also aligns manufacturing practices with global sustainability goals. In this evolving landscape, prioritizing environmental considerations in CNC machining is not just a regulatory requirement but also a significant competitive advantage in the global marketplace.
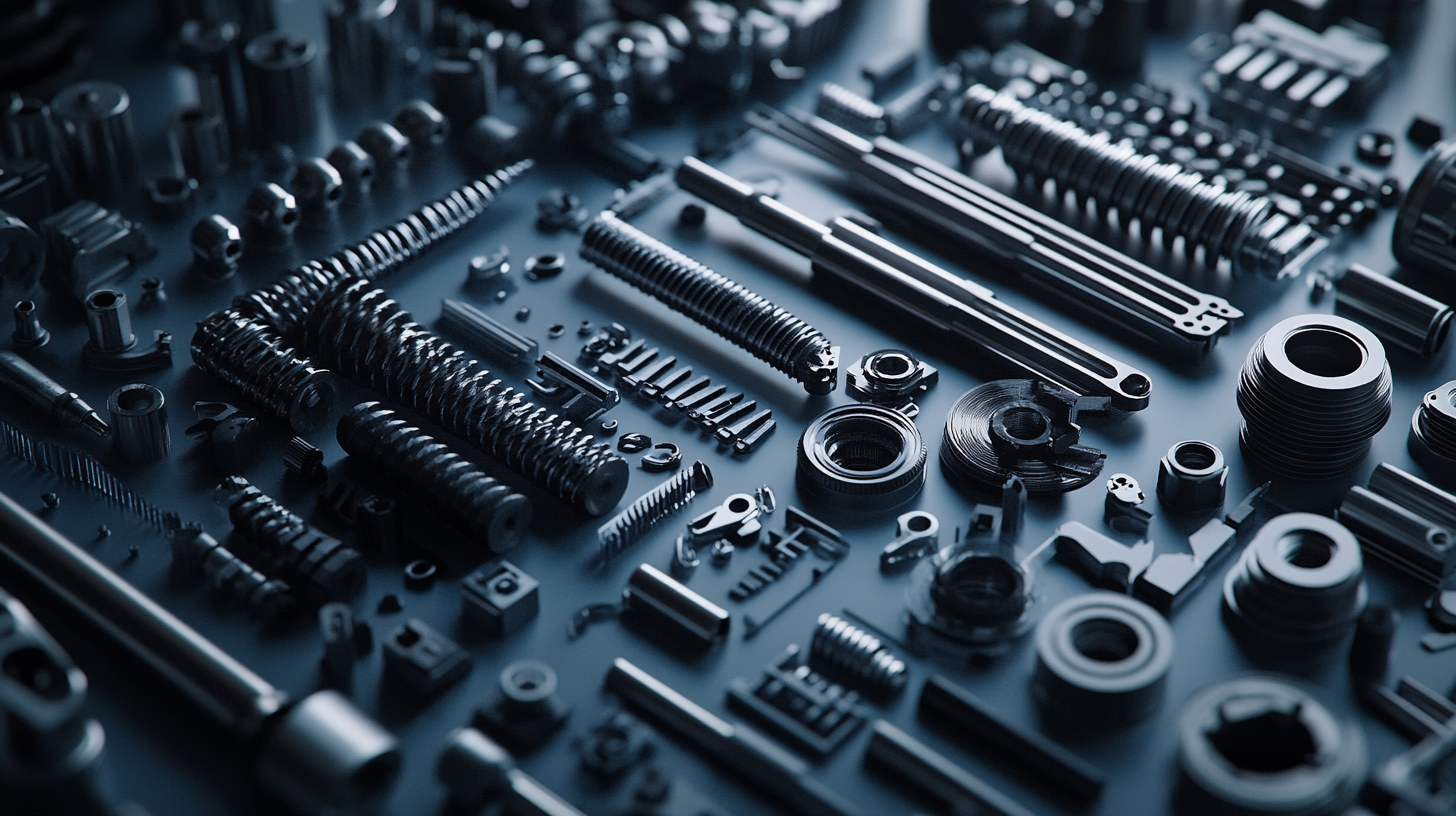
NORTH EASTON MACHINE • 218 Elm Street • North Easton, MA 02356 • 508-238-6219