Advantages of Choosing Quality Cnc Parts for Your Global Sourcing Needs
In today's rapidly evolving manufacturing landscape, businesses are increasingly recognizing the importance of sourcing high-quality CNC parts to maintain competitive advantage in global markets. According to a report by Grand View Research, the global CNC machining market is expected to reach $100 billion by 2025, driven by the relentless demand for precision-engineered components across various industries. Choosing quality CNC parts not only enhances the performance and reliability of machinery but also significantly reduces long-term operational costs. A study by MarketsandMarkets reveals that a mere 1% increase in production efficiency can translate to millions of dollars in savings annually for manufacturing firms. As companies navigate this complex global sourcing environment, prioritizing quality CNC parts can lead to improved product performance, reduced waste, and greater customer satisfaction, positioning organizations for sustainable success in the future.
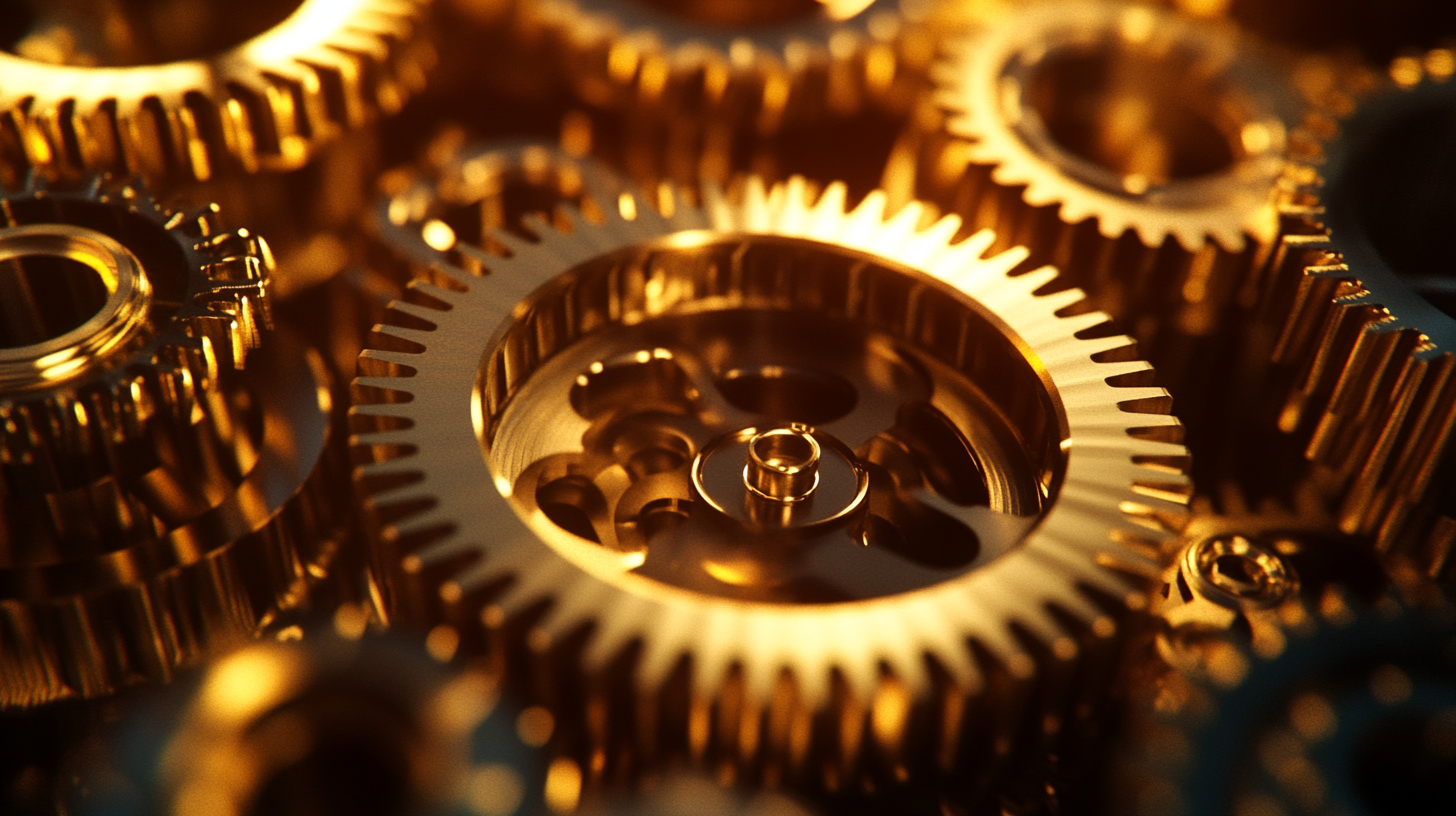
Benefits of High-Precision CNC Parts in Global Manufacturing
The rise of globalization has transformed the manufacturing landscape, making it essential for companies to obtain high-precision CNC parts to maintain competitiveness. According to a report by MarketsandMarkets, the global CNC machining market was valued at approximately $63 billion in 2020 and is projected to reach $100 billion by 2025, emphasizing a growing demand for sophisticated manufacturing solutions. High-precision CNC parts are crucial as they ensure superior tolerances and improve overall product quality, which is vital in sectors like aerospace and automotive where safety and reliability are paramount.
Investing in quality CNC parts can also lead to significant cost savings in the long run. A study conducted by Deloitte suggests that high-precision manufacturing can reduce operational costs by up to 25% through minimized material waste and fewer rework cycles. Furthermore, companies that prioritize quality in their CNC sourcing are more likely to experience timely delivery and higher customer satisfaction, essential factors in today’s fast-paced market. As organizations continue to navigate complex global supply chains, the choice of high-precision CNC components becomes not just a choice, but a strategic necessity for sustained success.
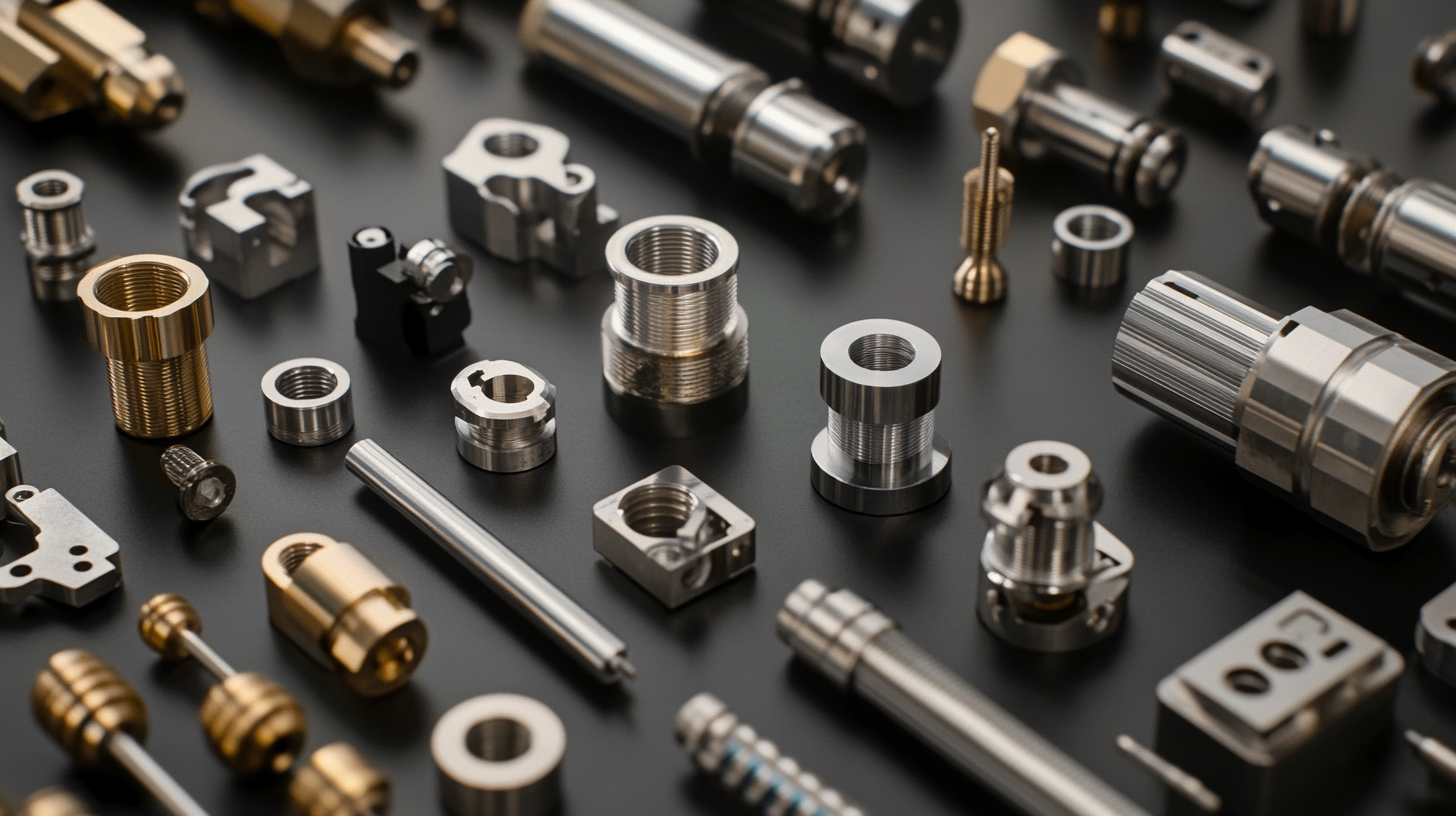
Cost Efficiency: Saving Money with Quality CNC Components
When it comes to global sourcing, the decision to choose quality CNC parts can significantly impact cost efficiency. While the initial investment may seem higher compared to cheaper alternatives, the long-term savings become evident over time. High-quality CNC components are produced with precision and durability, which minimizes the risk of defects and the need for frequent replacements. This reliable performance not only enhances production efficiency but also reduces downtime, allowing businesses to maintain a steady workflow and meet customer demands more effectively.
Moreover, quality CNC parts contribute to overall operational cost savings by improving the quality of the final products. When manufacturers use superior components, they experience fewer rework costs and lower warranty claims. Therefore, investing in quality translates to a better return on investment. As companies focus on their competitive edge in the global market, the choice of CNC parts becomes crucial. Opting for quality ensures that businesses can deliver products that meet high standards, ultimately driving customer satisfaction and loyalty, which are essential for sustained growth.
Advantages of Choosing Quality CNC Parts for Your Global Sourcing Needs
This chart illustrates the cost efficiency gained by utilizing quality CNC components compared to lower-grade alternatives. The data showcases potential savings across various industries when integrating high-quality CNC parts into their manufacturing processes.
The Role of CNC Technology in Reducing Production Time
CNC (Computer Numerical Control) technology has revolutionized the manufacturing landscape by significantly reducing production time, enhancing precision, and improving overall efficiency. By automating various processes, CNC machines allow manufacturers to minimize manual intervention, which not only speeds up production but also reduces the chances of human error. According to market research, the global CNC machining and turning centers market is expected to reach approximately USD 25.99 billion in 2023, growing at a compound annual growth rate (CAGR) of 6.6% from 2024 onwards. This growth highlights the increasing demand for advanced manufacturing solutions that CNC technology provides.
Furthermore, with the rising need for precision in metal and material fabrication, the CNC cutting machines market is projected to hit USD 11,671.4 billion by 2032. As businesses adopt more automated solutions, integrating CNC technology becomes crucial for staying competitive. These advancements are further bolstered by the emergence of AI in the manufacturing sector, which promises to enhance CNC processes even more by optimizing production workflows and increasing throughput. The fusion of AI with CNC technology marks a significant step forward in the evolution of precision manufacturing, establishing an efficient, effective, and innovative production environment.
Advantages of Choosing Quality CNC Parts for Your Global Sourcing Needs | ||
---|---|---|
Advantage | Description | Impact on Production Time |
Precision and Accuracy | CNC parts are manufactured with high precision, ensuring exact specifications. | Reduces rework and scrap rates, saving time. |
Consistency | Quality CNC parts maintain uniformity across production batches. | Minimal fluctuations in production times across batches. |
Reduced Material Waste | Efficient parts design reduces excess材料利用. | Less time and resources spent on material management. |
Faster Turnaround Times | Advanced CNC technology enables rapid manufacturing processes. | Significantly decreases overall production lead times. |
Cost Efficiency | Quality parts reduce the likelihood of failures and repairs. | Lower costs translate to reduced production timelines. |
Mitigating Risks: Quality Assurance in Global Sourcing of CNC Parts
When it comes to global sourcing of CNC parts, quality assurance is paramount. Companies must prioritize sourcing from suppliers that meet stringent quality standards to mitigate risks associated with production flaws. The complexities of modern supply chains compel businesses to look beyond cost considerations; they must effectively balance quality, reliability, and supply chain resilience. With increasing competition in various manufacturing sectors, including aerospace and electronics, ensuring high-quality CNC parts can make the difference between success and failure.
Additionally, as industries increasingly adopt advanced technologies like AI for manufacturing processes, the impact of sourcing high-quality components becomes even more critical. These technologies not only enhance production efficiency but also require precise and reliable parts to function optimally. By focusing on quality assurance in sourcing CNC parts, organizations can safeguard against potential disruptions, reduce the likelihood of costly recalls, and ultimately foster trust with their clients. As such, strategically selected partners that prioritize quality will empower businesses to thrive in an ever-evolving global marketplace.
Advantages of Choosing Quality CNC Parts for Global Sourcing
Enhancing Supply Chain Resilience with Reliable CNC Manufacturing
Choosing quality CNC parts is crucial for enhancing the resilience of supply chains, particularly in today’s dynamic manufacturing environment. The precision machining market is projected to reach USD 107.06 billion by 2030, with a compound annual growth rate (CAGR) of 7.8% from 2024 to 2030. This growth highlights the increasing reliance on high-quality components that can withstand supply chain disruptions and ensure operational continuity.
Investing in reliable CNC manufacturing not only streamlines production processes but also mitigates risks associated with supply chain vulnerabilities. Issues like supply chain spoofing, where malicious entities impersonate legitimate suppliers, stress the importance of securing partnerships with trusted manufacturers. Enhanced manufacturing practices, including the integration of digital technologies, can lead to better tracking and verification of components, further bolstering supply chain integrity.
Moreover, advancements in additive manufacturing provide significant opportunities for businesses seeking to improve resilience. These technologies can expedite prototyping and reduce dependency on traditional supply chains, particularly during times of uncertainty. By prioritizing quality CNC parts, companies can empower their supply chains to adapt swiftly to changes while maintaining high standards of quality and precision.
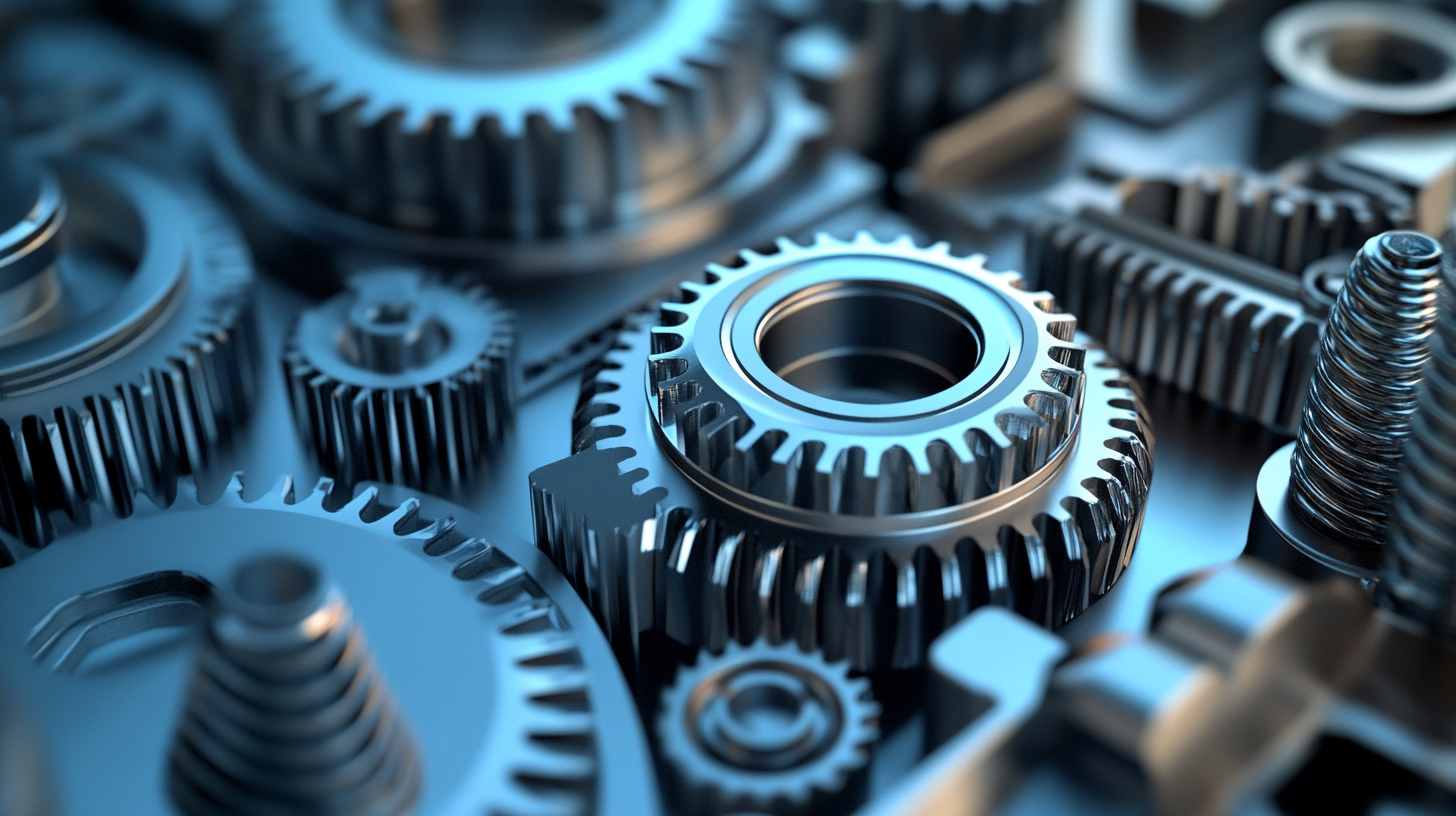
NORTH EASTON MACHINE • 218 Elm Street • North Easton, MA 02356 • 508-238-6219