Understanding the Advantages of CNC Milling and Turning Applications for Diverse Industries
In today’s rapidly evolving manufacturing landscape, CNC milling and turning have emerged as pivotal technologies that cater to a wide array of industries. These advanced machining processes not only enhance precision and efficiency but also offer significant advantages in terms of versatility and adaptability. As businesses strive to meet the demands of modern consumers, understanding the benefits of CNC milling and turning applications becomes crucial for maintaining a competitive edge. This blog will delve into the various aspects of these machining techniques and how they can be harnessed to improve production outcomes across different sectors.
CNC milling and turning empower manufacturers to achieve complex geometries and high tolerances that traditional methods may struggle to provide. From aerospace components to intricate medical devices, the implications of adopting these technologies are profound. By exploring specific case studies and industry examples, we aim to illuminate the transformative impact of CNC milling and turning on manufacturing processes. As we journey through the advantages these applications offer, it will become evident why they are essential in the toolkit of any forward-thinking manufacturer looking to innovate and thrive in a competitive market.
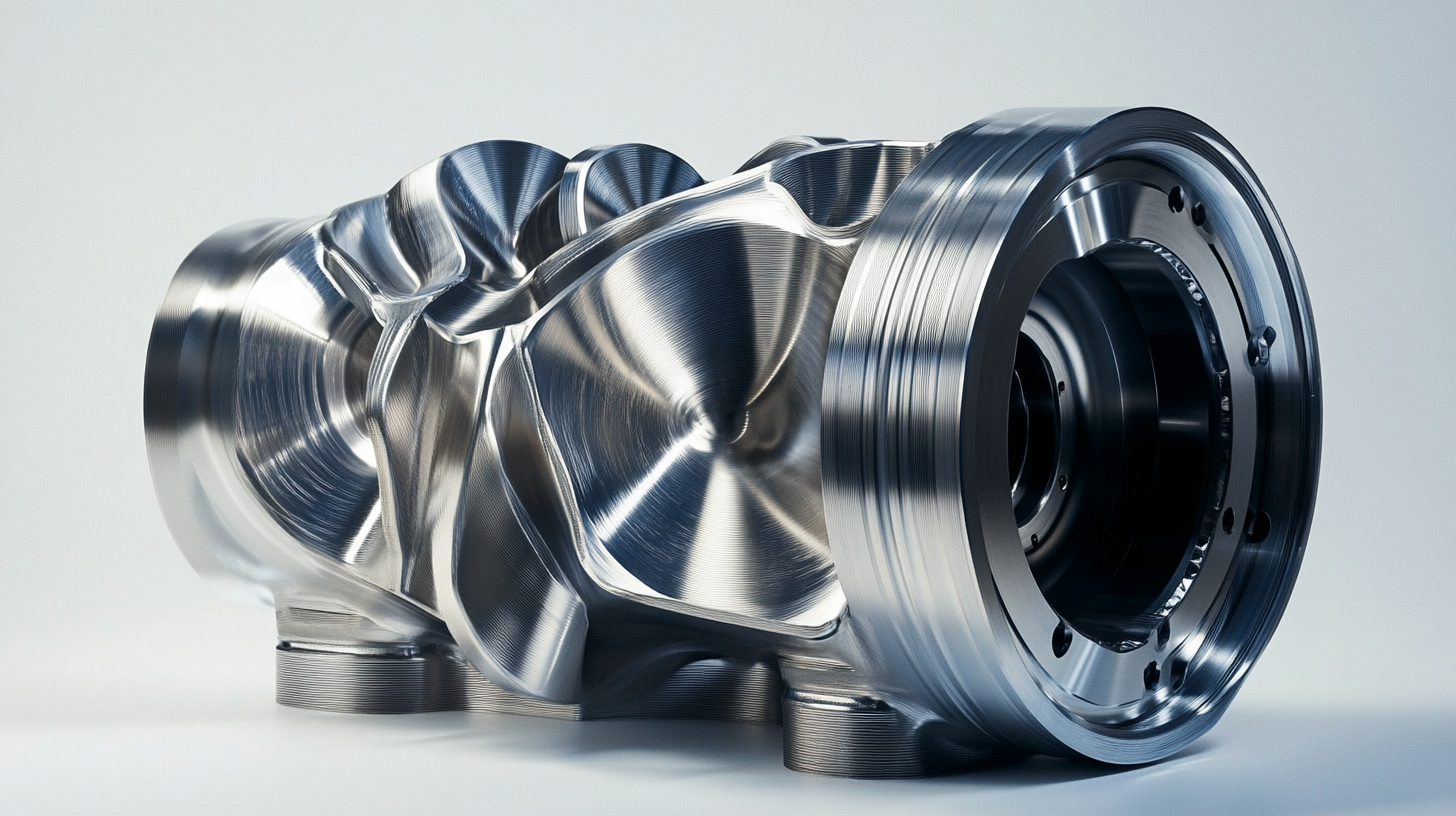
Exploring CNC Milling: Precision and Versatility in Manufacturing
CNC milling has emerged as a cornerstone of modern manufacturing due to its precision and versatility. This process allows manufacturers to create intricate components with remarkable accuracy, meeting the stringent demands of industries ranging from aerospace to medical devices. The advent of advanced CNC machines, including twin-spindle turning centers, has revolutionized the way these applications are performed. Such machines not only enhance production speed but also redefine the standards of precision, ultimately leading to superior product quality. The growing need for automation in manufacturing processes underscores the relevance of CNC milling and turning. As companies strive to increase efficiency while reducing operational costs, the ability to maintain high precision in machining becomes paramount. The integration of AI technologies further enhances the functionality of CNC equipment, paving the way for innovations in multi-axis machining centers. This trend is reflected in market analytics projecting significant growth in the CNC machine tools sector, driven by rising expectations for precision and flexibility in production. Recent collaborations and expansions in CNC services indicate an industry-wide commitment to advancing capabilities. By incorporating elements like broaching and offering full-spectrum support, companies are better positioned to cater to diverse manufacturing needs. As the landscape of CNC continues to evolve, the focus on precision and versatility will remain a key pillar in driving growth and innovation across various sectors.
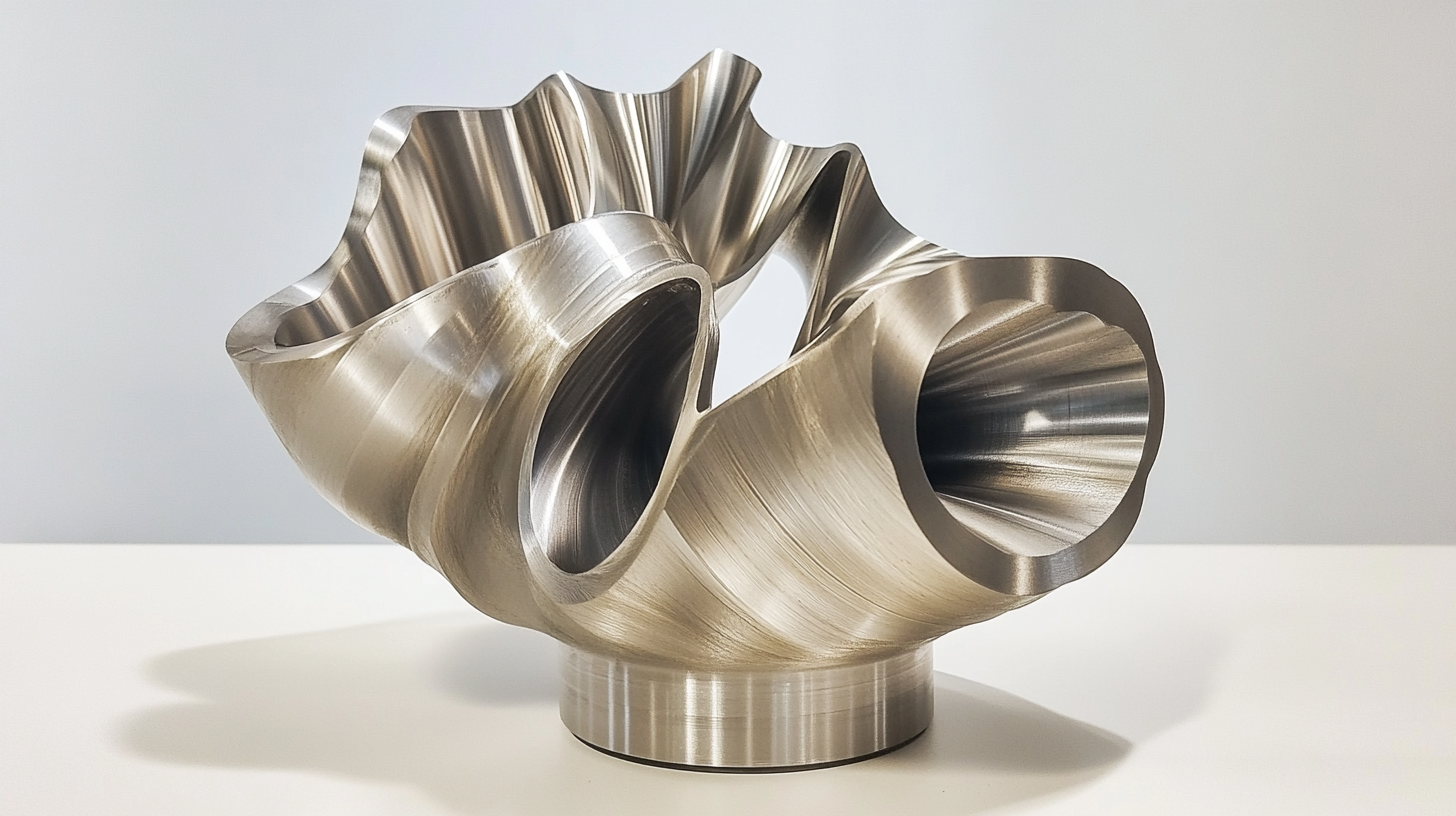
The Role of CNC Turning in Enhancing Production Efficiency
CNC turning has emerged as a crucial component in enhancing production efficiency across various industries, especially with the advent of next-generation technologies. As industries increasingly seek precision and automation, the global CNC machine tools market is projected to reach approximately USD 141.61 billion by 2032, driven by a growing demand for efficient manufacturing processes. This surge is not only a testament to the efficacy of CNC turning but also highlights its pivotal role in facilitating rapid production cycles.
The integration of artificial intelligence (AI) into CNC machining processes is set to revolutionize traditional manufacturing paradigms further. AI enhances precision, optimizes machining strategies, and reduces waste, thereby contributing to significant gains in efficiency. For instance, current research indicates a substantial growth rate of 7.8% in the precision machining market from 2024 to 2030, underscoring the transformative potential of incorporating advanced technologies into CNC operations.
Moreover, the diversity of materials being machined, including innovative composites such as LM25 aluminum reinforced with vanadium carbide, showcases the adaptability of CNC turning techniques. This adaptability not only meets the evolving demands of industries ranging from automotive to aerospace but also ensures that manufacturers can maintain high standards of quality and efficiency. As organizations continue to refine their production methodologies, CNC turning stands out as an indispensable tool in achieving manufacturing excellence.
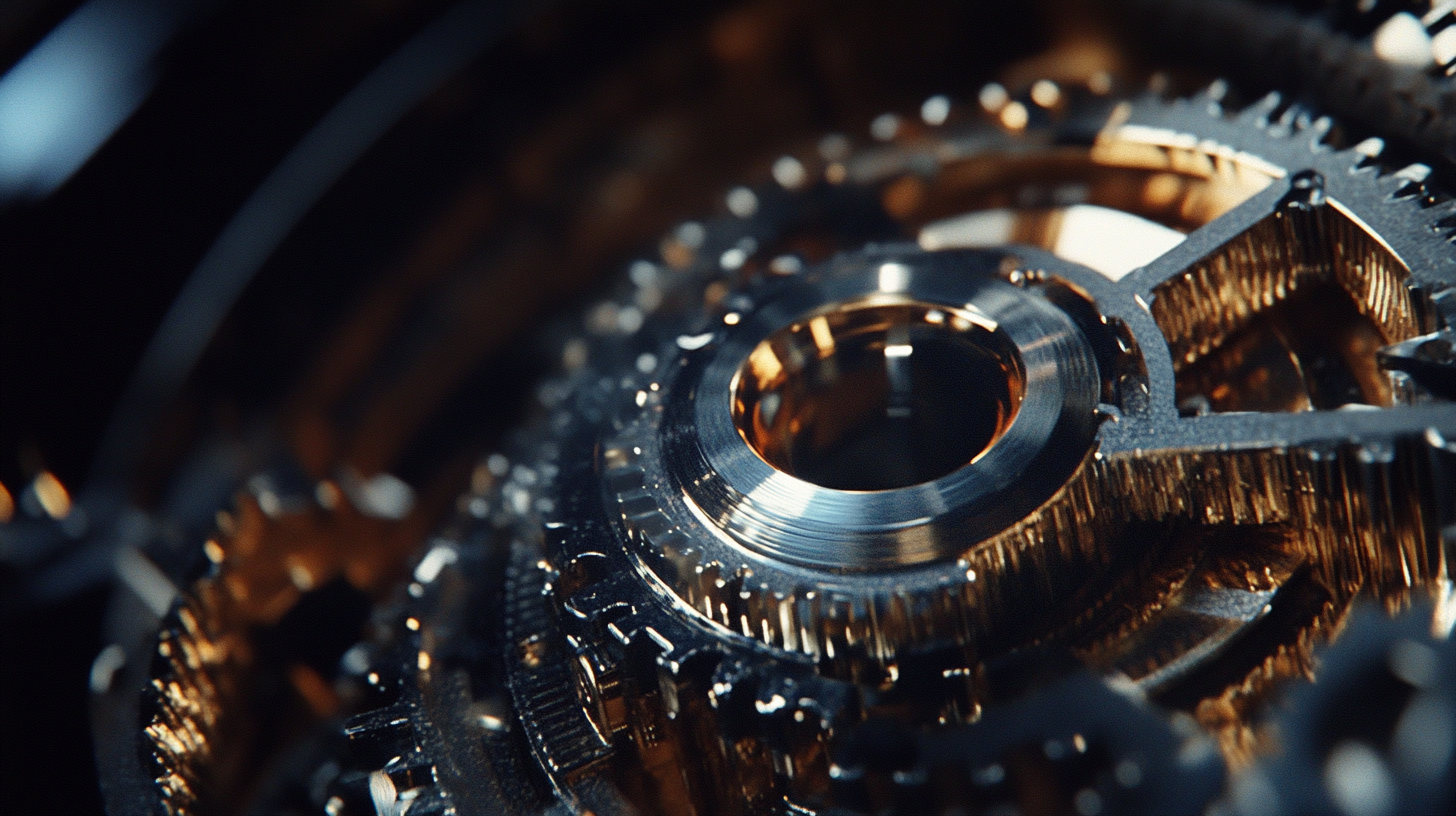
Key Industries Benefiting from CNC Machining Technologies
CNC machining technologies, encompassing CNC milling and turning applications, have become integral across various industries due to their precision and efficiency. Industries such as aerospace, automotive, medical, and electronics stand out as primary beneficiaries. For instance, the aerospace sector, which demands intricate designs and absolute reliability, relies heavily on CNC milling for producing components with tight tolerances. According to a report from Aerospace & Defense Technology, the global aerospace CNC machining market is expected to reach $4.2 billion by 2025, driven by the increasing production of aircraft and the need for lightweight, high-strength materials.
The automotive industry also significantly benefits from CNC machining technologies. With the rise in demand for electric and hybrid vehicles, manufacturers require advanced CNC milling and turning applications to create complex engine components and precision parts. A study published by Research and Markets highlights that the CNC machining market in the automotive sector is projected to grow at a CAGR of 7.5% from 2021 to 2026, highlighting the essential role of CNC technologies in efficient vehicle production and assembly lines.
Furthermore, the medical industry has seen a surge in the adoption of CNC machining, particularly for creating surgical instruments and implants. The ability to produce biocompatible materials with high accuracy is crucial in this field. The market for CNC machining in medical applications is estimated to grow to $1.8 billion by 2024, according to a report by Grand View Research. This growth is driven by advancements in technology and the pressing need for precision-engineered medical devices. In conclusion, these industries exemplify how CNC milling and turning applications enhance productivity, uphold quality standards, and drive innovation in manufacturing processes.
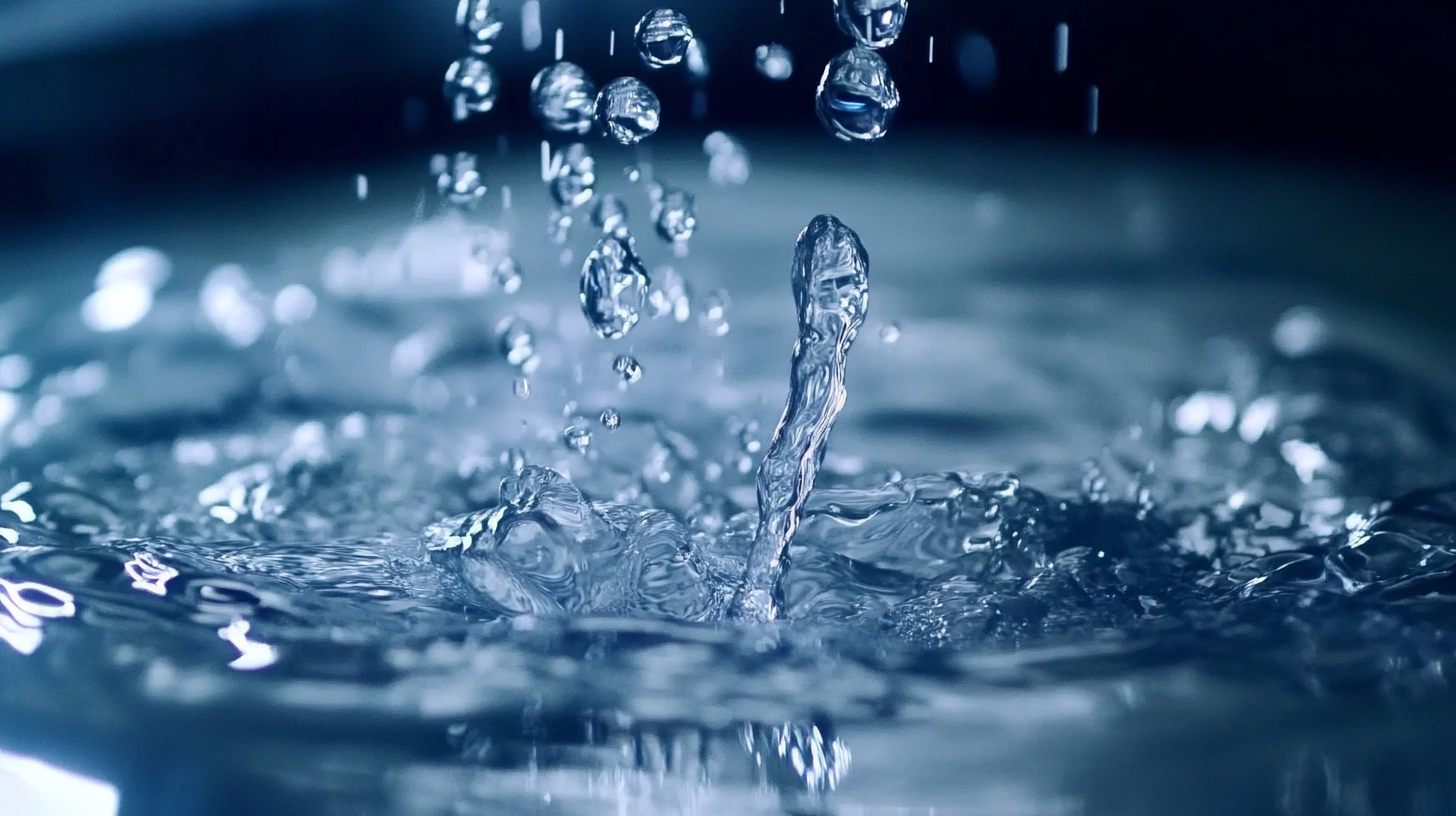
Comparative Advantages of CNC Milling vs. Traditional Methods
CNC milling and turning have revolutionized manufacturing processes across various industries, offering significant advantages over traditional machining methods. One of the most notable benefits of CNC milling is its precision. The automated nature of CNC machines allows for extremely tight tolerances and consistency, which is often difficult to achieve with manual processes. This precision results in higher quality products and reduces the need for secondary operations, ultimately saving time and resources.
In contrast, traditional machining methods often rely on the skill of the operator, which can introduce variables that affect product quality. While experienced machinists can produce excellent results, human error is an unavoidable risk that can compromise accuracy. Moreover, manual machining tends to be more time-consuming, requiring longer setup times and more frequent adjustments. CNC technology streamlines the entire process, enabling rapid production runs and greater efficiency, particularly for complex parts or high-volume orders.
Additionally, CNC milling and turning allow for more intricate designs that traditional methods struggle to replicate. The ability to program sophisticated geometries and perform multiple operations in one setup not only enhances the design possibilities but also significantly reduces lead times. This flexibility caters to the evolving demands of diverse industries, positioning CNC technology as the preferred choice for modern manufacturing.
Future Trends in CNC Applications Across Various Sectors
The future of CNC applications across various sectors is poised for transformative growth, driven by advancements in technology and the increasing demand for precision in manufacturing. As industries evolve, the integration of artificial intelligence (AI) within CNC systems is leading to significant breakthroughs. This trend not only enhances operational efficiency but also allows for more complex designs, which are crucial in competitive markets like consumer electronics. The shift towards digital twin technology in CNC machinery further emphasizes the need for high accuracy in production, especially in fields such as smartphone manufacturing where aesthetic appeal is paramount.
Additionally, the emphasis on sustainable practices within manufacturing is influencing CNC applications. With the growing focus on green intelligent manufacturing, industries are leveraging CNC technology to innovate while minimizing environmental impact. This fusion of smart technologies and sustainable practices will reshape how production lines operate, making them more eco-friendly while advancing productivity. The aluminum processing industry is already witnessing these trends, as it adapts to meet both performance requirements and market demands.
In sectors such as 3D printing, the incorporation of advanced materials like titanium is also opening new avenues for CNC applications. These developments reflect a broader movement towards enhancing manufacturing capabilities and optimizing product performance across diverse industries. As we look ahead, the continued evolution of CNC technology is expected to redefine production standards and operational strategies, ensuring it remains at the heart of industrial innovation.
NORTH EASTON MACHINE • 218 Elm Street • North Easton, MA 02356 • 508-238-6219